Welche sieben Herausforderungen im Bereich Lebensmittel und Getränke lassen sich durch Automatisierung lösen?
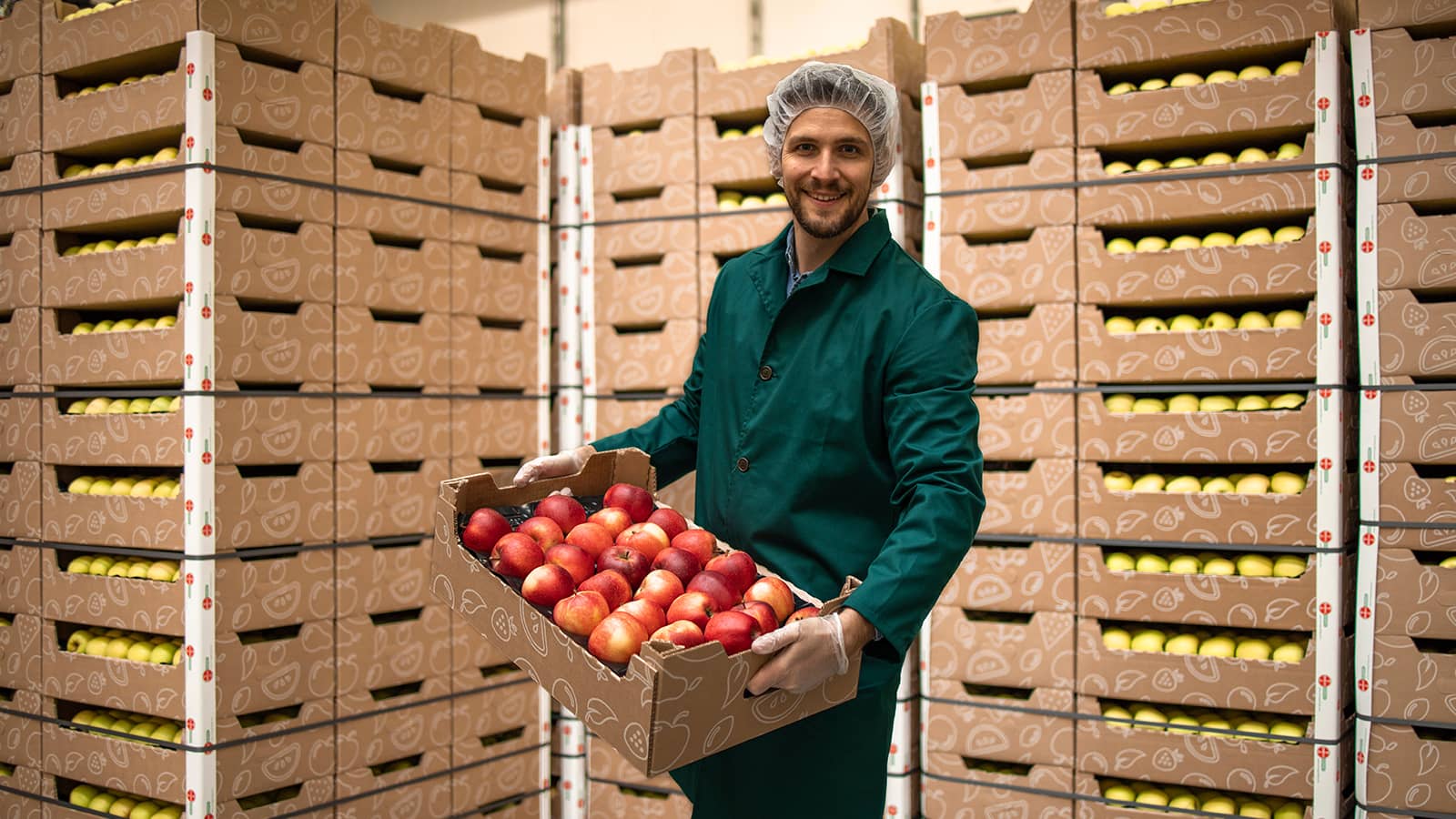
Marktherausforderungen
- Der Lebensmitteleinzelhandel übt Druck auf die Gewinnspannen der Lieferanten aus
- Die Verbraucher werden immer preisbewusster und erwarten gleichzeitig eine größere Produktpalette
- Die Inputkosten, einschließlich Arbeit, Rohstoffe und Energie, steigen
- Die Vorschriften für Sicherheit und Produktnachverfolgung werden immer strenger
Vorteile der Automatisierung
- Steigerung der Produktivität und Senkung der Kosten
- Verbesserung der Lagerkapazität
- Konsolidierung der Produktions- und Vertriebsabläufe
- Maximierung des Serviceniveaus durch Systemflexibilität und betriebliche Ausfallsicherheit
All diese Trends stellen erhebliche Herausforderungen für die Lieferkette und die Logistik dar.
Führende Hersteller und Händler der Lebensmittel- und Getränkeindustrie investieren in Automatisierungslösungen, um diese Herausforderungen zu bewältigen und um signifikante und dauerhafte Wettbewerbsvorteile für ihre Lieferketten zu erzielen.
Automatisierungslösungen sind die Grundlage für einen dauerhaften Wettbewerbsvorteil und bieten die notwendige Flexibilität, um die Herausforderungen des aktuellen Geschäftsumfelds zu meistern und sich auf die Zukunft vorzubereiten.
Herausforderung Nr. 1: Hohe Kosten und unzureichende Produktivität
Der Druck auf die Unternehmen wird nicht nur durch steigende Arbeitskosten erhöht. Auch die zunehmende Konzentration des Lebensmitteleinzelhandels und die immer preisbewussteren Verbraucher stellen eine Herausforderung dar.
Die Konzentration des Lebensmitteleinzelhandels drückt auf die Margen
Ein anhaltender Trend ist die Konzentration des Lebensmitteleinzelhandels, d. h. eine immer geringere Anzahl von Einzelhändlern nimmt eine immer dominantere Stellung ein. In Australien beispielsweise lag der Marktanteil der beiden größten Lebensmittelhändler im Jahr 2013 bei 73 %. Diese Zahl ist im Jahr 2021 auf 65 % gesunken.
Auch im Spirituosenhandel haben die großen Lebensmittelhändler ihren Marktanteil konsolidiert. Die beiden größten Lebensmittelhändler haben große Spirituosengeschäfte eröffnet und praktizieren eine aggressive Preisgestaltung. Dadurch kontrollieren sie aktuell 57 % des Einzelhandelsmarktes für Alkohol.
Ferner haben sie ihre Marktposition genutzt, um starke Vereinbarungen mit den Lieferanten zu treffen, die die Gewinnspannen der Lieferanten erodieren und es den Lebensmittelhändlern ermöglichen, niedrige Ladenpreise anzubieten, mit denen kleine Geschäfte nur schwer konkurrieren können. Außerdem nutzen sie ihre Position, um ihre eigenen Handelsmarken auf Kosten von Markenprodukten zu vertreiben.
Lebensmitteleinzelhändler verlagern ihre Bestände zurück zu den Herstellern
Auch verlagern große Lebensmitteleinzelhändler ihre Bestände zurück zu den Lieferanten, was die Logistikkosten für Hersteller und Vertriebsunternehmen erhöht – insbesondere für diejenigen, die ihren Vertrieb an externe Logistikpartner ausgelagert haben. Da die Lebensmittelhändler ihre Bestände an die Lieferanten zurück verlagern, halten die externen Logistikunternehmen höhere Bestände vor, was für viele ihrer Kunden aus der verarbeitenden Industrie mit entsprechenden Kosten verbunden ist.
Infolgedessen sind Hersteller und Händler zunehmend bestrebt, ihre Logistikoperationen auszulagern und die Kompetenz für die Lieferkette wieder in ihr eigenes Geschäft zu integrieren. Für viele ist jetzt die ideale Gelegenheit, ihre Vertriebsaktivitäten zu optimieren.
Preisbewusste Verbraucher
Die Verbraucher sind nach wie vor sehr preisbewusst und ziehen Supermärkte mit günstigen Artikeln Mini-Märkten vor. Dies hat zur Folge, dass Inhaber von kleinen Geschäften und kleine Lebensmitteleinzelhändler mit höheren Margen von dieser Verlagerung erheblich betroffen sind, da Lebensmitteleinzelhändler mit niedrigeren Margen ihre Gewinne kompensieren.
Die Verbraucher sind immer offener für den Kauf neuer und erweiterter Produkt- und Markenpaletten und betrachten Handelsmarken als gute Alternative zu nationalen Marken. Viele sind heute der Meinung, dass Handelsmarken die gleiche Qualität haben wie traditionelle Haushaltsmarken. Dieser Trend setzt die Gewinnspannen im Lebensmittel- und Getränkesektor weiter unter Druck, da die Unternehmen die Preise ihrer Marken senken müssen, um wettbewerbsfähig zu bleiben.
Arbeit: Steigende Kosten, sinkende Verfügbarkeit
Die alternde Bevölkerung und die zunehmende Abneigung der Arbeitskräfte, in Lagern zu arbeiten, insbesondere in Kühl- und Gefrierhäusern, haben die Verfügbarkeit von Arbeitskräften eingeschränkt und gleichzeitig die Arbeitskosten in die Höhe getrieben. Dies hat erhebliche Auswirkungen auf die Gesamtkosten des Vertriebs.
Während die Erzeuger ihre Verarbeitungsprozesse automatisiert haben, sind Vertrieb und Lagerhaltung bei vielen weiterhin sehr arbeitsintensiv. In den letzten Jahren haben Unternehmen in verschiedenen Sektoren die Arbeitsproduktivität erhöht, indem sie ihre Belegschaft aufgestockt haben. Viele erkennen nun, dass der nächste Schritt zur Verbesserung der Arbeitsproduktivität darin besteht, in automatisierte Technologie zu investieren.
Lösung
Mit einem ASRS die Produktivität steigern und die Kosten senken
Ein automatisiertes Lager- und Bereitstellungssystem (Automated Storage and Retrieval System, ASRS) automatisiert den Prozess der Produktlagerung und -handhabung vollständig und macht „Berührungen“ durch das Personal überflüssig, was die Arbeits- und Betriebskosten im Lager erheblich reduziert. Obwohl dies in hohem Maße vom spezifischen Bestandsprofil des jeweiligen Herstellers abhängt, lassen sich mit einem ASRS in der Regel Produktivitätssteigerungen von 20 bis 30 % erzielen.
Das System reduziert auch Abfall sowie Produkt- und Regalschäden, die von Gabelstaplern verursacht werden, und hat in der Regel einen geringeren Wartungsbedarf im Vergleich zu Leasing- und Wartungskosten für Gabelstapler.
Herausforderung Nr. 2: Verfügbarkeit von Grundfläche
Als Reaktion auf den Kostendruck besteht bei Herstellern und Händlern ein zunehmender Trend zur Konsolidierung ihrer Standorte. Durch die Verringerung der Vertriebsstellen in ihren Netzen können Unternehmen sowohl die Lager- als auch die Transportkosten senken. Im Rahmen dieser Konsolidierung errichten Lebensmittel- und Getränkehändler ihre Distributionsbetriebe in unmittelbarer Nähe ihrer Produktionslinien, wodurch der kostspielige und arbeitsintensive Prozess des Transports von Fertigwaren von der Verarbeitungsanlage zum Lager entfällt.
Die begrenzte Verfügbarkeit von Grundfläche in der Nähe von Produktionsanlagen und die steigenden Grundstückskosten – insbesondere in Ballungszentren – können jedoch dazu führen, dass herkömmliche manuelle Lager- und Transportlösungen nicht mehr ausreichen.
Lösung
Mit einem automatisierten Lager die Lagerdichte erhöhen und den Flächenbedarf senken
Mit der Einführung einer Automatisierungslösung können Gebäudehöhe und Grundfläche optimal genutzt werden. Durch die Maximierung der Lagerdichte und die Möglichkeit, Höhen von bis zu 35 m zu erreichen, benötigen Paletten-RBG-Systeme bis zu 60 % weniger Platz als herkömmliche Palettenlager.
Dank des geringeren Platzbedarfs können Hersteller mit automatisierten Vertriebseinrichtungen in der Nähe ihrer Produktionsstätten errichten – selbst dort, wo nur wenig Grundfläche verfügbar ist. Und durch die Konsolidierung des Vertriebs in einem automatisierten Lager können Hersteller die Anforderungen an die Lagerhaltung und die Gesamtinventarkosten senken.
Auch für herkömmliche Lager, in denen der Platz knapp wird, ist das automatisierte Lager eine kosteneffiziente Lösung. Wenn Sie herkömmliche Palettenregale durch RBGs ersetzen, können Sie:
- die Lagerkapazität für Paletten signifikant erhöhen,
- die Lebensdauer des bestehenden Gebäudes verlängern
- die Gemeinkosten senken
- die Kosten und Betriebsunterbrechungen vermeiden, die mit dem Bau einer neuen Einrichtung oder einem Umzug verbunden sind
Herausforderung Nr. 3: Sicherstellung eines hervorragenden Kundendienstes
In einem derart wettbewerbsintensiven, verbraucherorientierten Markt ist es für Lebensmittel- und Getränkehersteller wichtiger als für jede andere Branche, das richtige Produkt in der richtigen Menge und zum richtigen Zeitpunkt zu den Kunden zu bringen. Lebensmittelhändler tolerieren keine verpassten Liefertermine oder falsche Produkte. Eine nicht gelieferte Sendung oder auch nur eine fehlende Palette kann dazu führen, dass die Regale in den Geschäften nicht mehr gefüllt sind und Vertragsstrafen für verspätete oder unvollständige Lieferungen verhängt werden. Der Vertrieb muss sicherstellen, dass er das richtige Produkt in der erforderlichen Menge vorrätig hat und dass die Lieferungen vollständig sind und rechtzeitig versandt werden. Außerdem müssen die Vertriebsfunktionen sicherstellen, dass sie keine Engpässe in den Betriebsabläufen verursachen, die zum Stillstand von Produktionslinien führen können. Und all dies muss auf möglichst kostengünstige Weise erreicht werden.
Lösung
Mit einem automatisierten Lager die Servicequalität optimieren
Durch die vollständige Automatisierung der Einlagerungs-, Lagerungs- und Auslagerungsprozesse eliminiert das automatisierte Lager potenzielle Bedienerfehler und gewährleistet eine optimale Bestandsverfügbarkeit und maximale Auftragsgenauigkeit. Der Betrieb weiß genau, was auf Lager ist, und die Kundenbestellungen werden während des gesamten Prozesses vor der Lieferung überprüft.
Das automatisierte Lager bietet auch erhebliche Vorteile für Bereitstellungs- und Versandanwendungen sowie für konsolidierte Produktions- und Distributionsverarbeitungslinien – alles entscheidende Elemente, um sicherzustellen, dass Kundenaufträge genau und rechtzeitig erfüllt werden.
Mit dem automatisierten Lager eine effiziente Bereitstellung und Abfertigung sicherstellen
In einem manuellen Bereitstellungs- und Versandbereich müssen die Paletten in Mengen von Anhängerladungen bereitgestellt werden, damit die Lkw schnell beladen werden können. Ein ausreichend großer Abfertigungsbereich ist für die Bewältigung der täglichen Betriebsschwankungen von entscheidender Bedeutung. Viele Dockbereiche haben jedoch nur eine begrenzte Grundfläche und die Gebäudehöhe wird nicht optimal genutzt (im Gegensatz zu einem automatisierten Lager). Im Falle einer Störung, z. B. einer Lkw-Panne auf dem Weg zum Werk, bleiben die Bestände für Bestellungen oft im Versand, bis das Problem behoben ist. Dies kann zu potenziellen Engpässen bei anderen Aufträgen führen, was wiederum zu Unterbrechungen in vorgelagerten Prozessen führen kann. Und dies kann erhebliche Auswirkungen auf die Auslieferung von Kundenaufträgen haben.
Eine wirksame Alternative ist die Ausweitung der Nutzung der RBG-Technologie auf die Bereitstellung und den Versand. Da ein automatisiertes Lager schnellere Zykluszeiten als manuell betriebene Gabelstapler bietet, können die Paletten aus dem System ausgelagert werden, sodass sie bei Ankunft des Transportfahrzeugs bereit zum Beladen sind. Dadurch, dass das automatisierte Lager Zonen für die Vorlagerung von Aufträgen nutzt, können Lieferungen schnell und effizient versendet werden, indem der schnellste Zugang zu den Lagerplätzen ermöglicht wird. So wird sichergestellt, dass Kundenbestellungen innerhalb sehr kurzer Zeitfenster geliefert werden können.
Fahrerlose Transportfahrzeuge (Fahrerlose Transportfahrzeuge, AGV): Die Integration von Verarbeitungslinien mit AGVs und ASRS erhöht die Zuverlässigkeit
Für Produktions- und Vertriebseinrichtungen hat die durchgängige Automatisierung des Auftragsabwicklungsprozesses erhebliche Vorteile. Lösungen, die eine Vielzahl von Optionen wie Palettierung oder ASRS umfassen, erhöhen die Geschwindigkeit und Belastbarkeit von repetitiven Aufgaben und verhindern, dass Engpässe in kritischen Prozessen entstehen.
Während Palettenförderer eine robuste und zuverlässige Verbindung zwischen Produktion und automatischer Lagerung bieten, sind AGVs die ideale Lösung für Betriebe, die ein Höchstmaß an Konsistenz und Flexibilität für verschiedene Bereiche des Lagers benötigen. Abgesehen davon, dass AGVs einen zuverlässigen und kosteneffizienten Palettentransport bieten, sind sie äußerst flexibel, sodass die Wege problemlos angepasst und zusätzliche AGVs in die Flotte aufgenommen werden können, wenn sich die Durchsatzanforderungen und die Abhol- und Lieferziele ändern.
Herausforderung Nr. 4: Eine steigende Anzahl der Bestandseinheiten (SKU) pro Artikel und Komplexität der Bestellung
Die Verbraucher erwarten eine breitere Produktpalette, die vom individuellen Geschmack, von Trends und von Fitness- und Gesundheitsaspekten bestimmt wird. Ein Beispiel dafür ist die Abkehr von Bier, Milch und Erfrischungsgetränken, die mit einem Anstieg des Konsums von Craft-Bieren, Apfelwein, Sojamilch und Gesundheitsgetränken einhergeht. Die Unternehmen reagieren auf die Nachfrage der Verbraucher mit der Einführung zahlreicher neuer Produkte.
Das führt dazu, dass die Lebensmittel- und Getränkehersteller die Anzahl von Bestandseinheiten pro Artikel in ihren Lieferketten erhöhen und eine immer größere Produktvielfalt vorrätig haben müssen. Für diejenigen, die auch Eigenmarken für Einzelhändler herstellen, erhöht dies nur die Komplexität der zu verwaltenden Lagereinheiten.
In einem manuellen Lagersystem bedeutet die Handhabung zusätzlicher Artikel, dass alles größer werden muss – mehr Palettenlager, mehr Kommissionierplätze und mehr Wege, was zu langsameren und weniger effizienten Abläufen in größeren, teureren Lagern führt.
Lösung
Die ASRS-Technologie bietet eine größere Lagerkapazität für die Handhabung einer größeren Anzahl von Lagereinheiten
Durch die größere Lagerdichte bis zur Deckenhöhe bietet das ASRS den Betrieben deutlich mehr Lagerplätze für die Handhabung zusätzlicher Artikel ohne längere Wege. Da sich die Auftragsprofile ändern und auch der Durchsatz einzelner Artikel schwankt, kann die ASRS-Technologie die Produkte so umschichten, dass die Schnelldreher näher an den Ausschleusungszonen platziert werden. Dies führt zu einer besseren Reaktionsfähigkeit des Systems.
Herausforderung Nr. 5: Management von Gesundheit und Sicherheit am Arbeitsplatz
Gesundheit und Sicherheit am Arbeitsplatz haben für die meisten Lebensmittel- und Getränkehersteller oberste Priorität. Das Bewegen und Lagern schwerer Palettenladungen und die Gefahr von Bruchschäden und Verschüttung stellen eine Gefahr für das Personal dar.
Unfälle mit Ausfallzeiten werden für Unternehmen immer kostspieliger, und eine alternde Belegschaft macht die Bewältigung der Herausforderungen im Bereich des Arbeitsschutzes noch dringlicher.
Lösung
Ein ASRS minimiert Risiken für den Arbeitsschutz
Dadurch dass bei einem ASRS Bediener und Gabelstapler wegfallen, werden die Arbeitsschutzrisiken deutlich reduziert, die mit einer manuellen Handhabung verbunden sind.
Die ASRS-Technologie arbeitet mit einer präzisen Ein- und Auslagerung von Lagerplätzen, wodurch kein Risiko von Produkt-, Paletten- oder Regalbeschädigungen mehr besteht. Das ASRS kann auch Palettenladungen in der genauen, von einem Host-System vorgegebenen Reihenfolge entsprechend den Achslastanforderungen an einen Anhänger liefern.
Herausforderung Nr. 6: Steigende Energiekosten
Steigende Energiekosten wirken sich auch auf die Gewinnspannen im Lebensmittel- und Getränkesektor aus. Dies ist von besonderer Bedeutung für Produzenten mit energieintensiven Kühlhäusern.
Lösung
Mit einem ASRS den Gesamtenergieverbrauch senken
Durch die Maximierung der Lagerdichte und die Optimierung des Platzbedarfs reduziert ein ASRS den Energiebedarf für die Kühlung oder Erwärmung des Lagerbereichs. Dies ist in temperaturkontrollierten Einrichtungen besonders wichtig, denn dort führt eine Verringerung des zu kühlenden Raumes zu einer erheblichen Senkung des Energieverbrauchs. ASRS-Systeme benötigen auch weit weniger Beleuchtung als der manuelle Betrieb, was den Energieverbrauch weiter senkt.
Ausgestattet mit einer Energierückgewinnungstechnologie spart die Dematic ASRS-Technologie auch im täglichen Betrieb Energie. So wird beispielsweise die Bremsenergie zurückgewonnen und vom Hubmotor genutzt, wodurch unser ASRS bis zu 29 % weniger Energie verbraucht als die herkömmliche ASRS-Technologie.
Herausforderung Nr. 7: Anforderungen im Bereich der Produktnachverfolgung
Die staatlichen Behörden für Lebensmittelsicherheit verlangen, dass Lebensmittel in allen Stufen der Produktion, der Verarbeitung und des Vertriebs (auch bekannt als „vom Erzeuger zum Verbraucher“) überwacht werden. Damit soll verhindert werden, dass kontaminierte Produkte zu den Verbrauchern gelangen, und es sollen schnelle und wirksame Abhilfemaßnahmen ermöglicht werden, falls etwas schief geht, z. B. bei Produktrückrufen.
Systeme für das Management der Lieferkette müssen die Herkunft von Rohstoffen, Zusatzstoffen und allen anderen Eingängen erfassen, bevor sie mit Chargen-/Loskennzeichnung sowie Produktions- und Verfallsdatum gekennzeichnet werden. Lebensmittel- und Getränkehersteller halten damit nicht nur die Lebensmittelsicherheitsstandards ein. Sie haben auch erkannt, dass Produktrückverfolgbarkeitssysteme zum Schutz ihrer Marken beitragen, denn sie ermöglichen es, schnelle und effektiv auf jeden Vorfall zu reagieren. Neben der Chargen- und Losverfolgung müssen Lagerverwaltungssysteme (Warehouse Management Systems, WMS) den Bestand und die FIFO-Regeln (First-In-First-Out) effektiv verwalten. In vielen Fällen akzeptieren die großen Lebensmittelhändler nur fortlaufend nummerierte Chargen und Verfallsdaten.
Lösung
Ein ASRS in Kombination mit einem Warehouse Control System (WCS) bietet umfassende Verfolgungs- und Reaktionsmöglichkeiten
Die ASRS-Technologie kann über ein Warehouse Control System (WCS) vollständig in ein Unternehmens-/Produktionsressourcenplanungssystem (Enterprise/Manufacturing Resource Planning, ERP) oder ein Warehouse Control System (WCS) integriert werden. Das WCS ermöglicht die präzise Verfolgung von Produktbewegungen und Lagerorten in Echtzeit. Als Teil seiner umfassenden Bestandsverfolgungsfunktionen verwaltet das WCS die Chargen- und Losverfolgung von Produkten und verwaltet außerdem in Verbindung mit dem Host die First-In-First-Out (FIFO)- und First-In-Last-Out (FILO)-Regeln.
Das WCS integriert auch nahtlos andere Systeme im Lager, darunter:
- Palettierung
- Förderanlagen
- AGV
- Palettentransport
- Kommissionierung (robotergesteuert und sprachgesteuert)
Durch die Integration von Technologien erhalten Unternehmen eine vollständige Systemverwaltung und einen Überblick über den gesamten Betrieb. Im Falle eines Zwischenfalls, z. B. eines Produktrückrufs, kann das Management sofort die betreffenden Chargen oder Lose identifizieren und das System beauftragen, entsprechende Maßnahmen zu ergreifen, z. B. das Produkt an einen bestimmten Standort zu bringen.
Lesen Sie mehr darüber, wie Dematic Software für Sie arbeiten kann und einen Mehrwert für Ihr Unternehmen schafft.
Die Vorteile von Dematic
Die neuesten Entwicklungen in der ASRS-Technologie in Kombination mit den Dematic Software-Lösungen bieten erhebliche Vorteile für Lebensmittel- und Getränkeproduzenten, die sich den Herausforderungen ihrer Vertriebsaktivitäten stellen wollen.
Mit den Lösungen von Dematic können die Lebensmittel- und Getränkeunternehmen ihre gesamten Produktions- und Lieferkettennetzwerke überprüfen und herausfinden, wo sie Lagerung und Vertrieb konsolidieren können, um die Gesamtkosten zu senken und ihren Betrieb zu optimieren. Da die Kosten für die Automatisierung in den letzten Jahren erheblich gesunken sind, waren der Geschäftsnutzen und die Investitionsrentabilität noch nie so groß wie heute.