Das Lagerhaus mit Temperaturregulierung
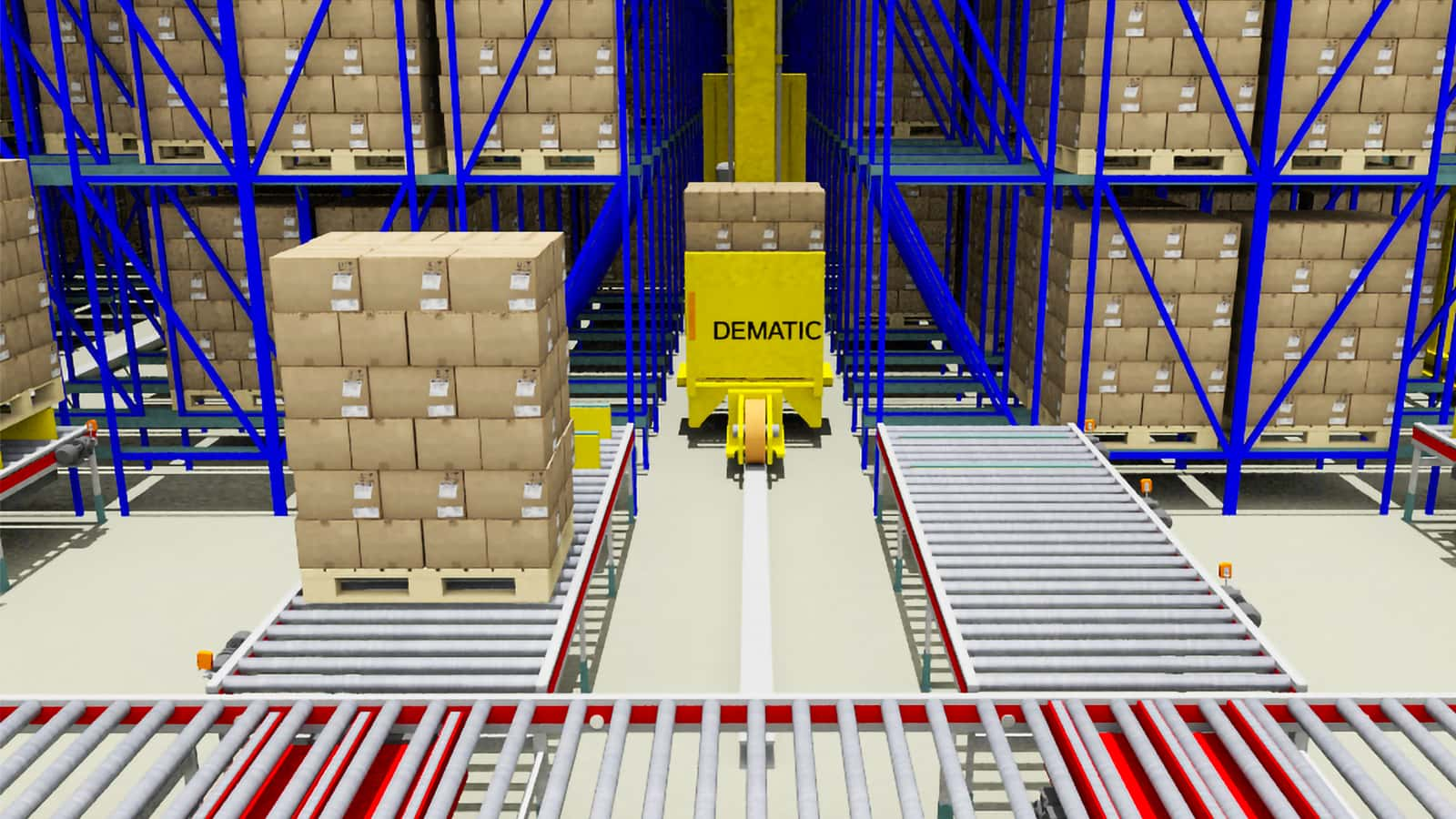
Automatisierung im Vergleich mit herkömmlichen Lagerhäusern
Die Automatisierung von Lagerhäusern mit Temperaturregulierung (Kühl- oder Gefrierkammern) ist heutzutage lohnender denn je. Immer mehr Anbieter für den Lebensmittel- und Getränkevertrieb stellen das Konzept ihrer herkömmlichen Lagerhäuser in Frage. Im Vergleich zu herkömmlichen Lagerhäusern mit Temperaturregulierung bietet die Automatisierung folgende Vorteile:
Smaller building footprint in less cubic space
Because automated warehouse can more readily include a high bay configuration to take advantage of vertical space, they require a smaller building footprint — typically 25% of the size of a traditional warehouse. Again, because automated warehouses do not need to accommodate manual access, they can be configured with a higher density design, so less cubic space is required for the same amount storage — typically 25% to 35% more storage capacity over traditional warehouses.
Energy savings
The high-density configuration of automated warehouses reduces energy operating costs — more storage in less refrigerated space. Also, automated warehouses tend to have less roof space (where most energy lost). You can expect energy costs to be 35% to 50% less with automated warehouses.
The doors to the temperature-controlled areas of automated warehouses can be smaller and used more strategically, which reduces energy use. Another energy savings: Traditional warehouse defrosts once per day — automated warehouse defrosts once per week.
Minimized worker exposure to harsh environment
The temperature-controlled areas of automated warehouses do not require workers to be present. Elimination of labor in the harsh freezer environment results in improved labor productivity and greatly reduced worker recruitment and retention issues. (Turnover rates for freezer environment positions are quite high.)
Reduced damage/better safety
Automated warehouses reduce or eliminate the need for manually operated forklift trucks, which greatly decreases the opportunities for damage to racks, product, and freezer doors and the costs to repair them. For example, it is not unusual for a traditional warehouse to need to replace a freezer door once per month due to forklift truck damage.
In addition, manually operated forklift trucks in traditional warehouses create potential safety hazards for workers who share the aisles and workspaces. The is no need for workers to share the aisles in automated warehouses.
Improved inventory and order accuracy
Digital control of inventory in automated warehouses eliminates location errors that occur in traditional warehouses with the manual forklift trucks putting inventory incorrectly. Improved inventory accuracy is especially a selling feature for 3PL freezer warehouse operations. Prospective 3PL customers depend on service providers that can guarantee extremely high inventory accuracy.
Accurate inventory leads to accurate orders with automated warehouses providing nearly perfect order fulfillment rates with features such as inline weigh scales that verify load weights in real time. Traditional warehouses can experience several picking errors per day. Automated systems may experience a picking error once per month. Inaccurate orders can be costly. A wrong order delivered to a customer can create the need for an emergency expedited delivery.
Improved quality control
Automated warehouses systematically control product freshness by rotating inventory on a first-in, first-out (FIFO) basis. This greatly reduces issues with expired products. With traditional warehouses, forklift truck operators may not always pick the right inventory first when performing order fulfillment tasks. In addition, if inventory needs to be quarantined, an automated systems can programmatically lock it in a designated area to keep it separate from the other inventory.
With the automated system, inventory pallets are optimally spaced for ideal circulation of freezer air to ensure ideal storage conditions.