Adidas punktet mit einem automatisierten Distributionszentrum und schützt seine Marke
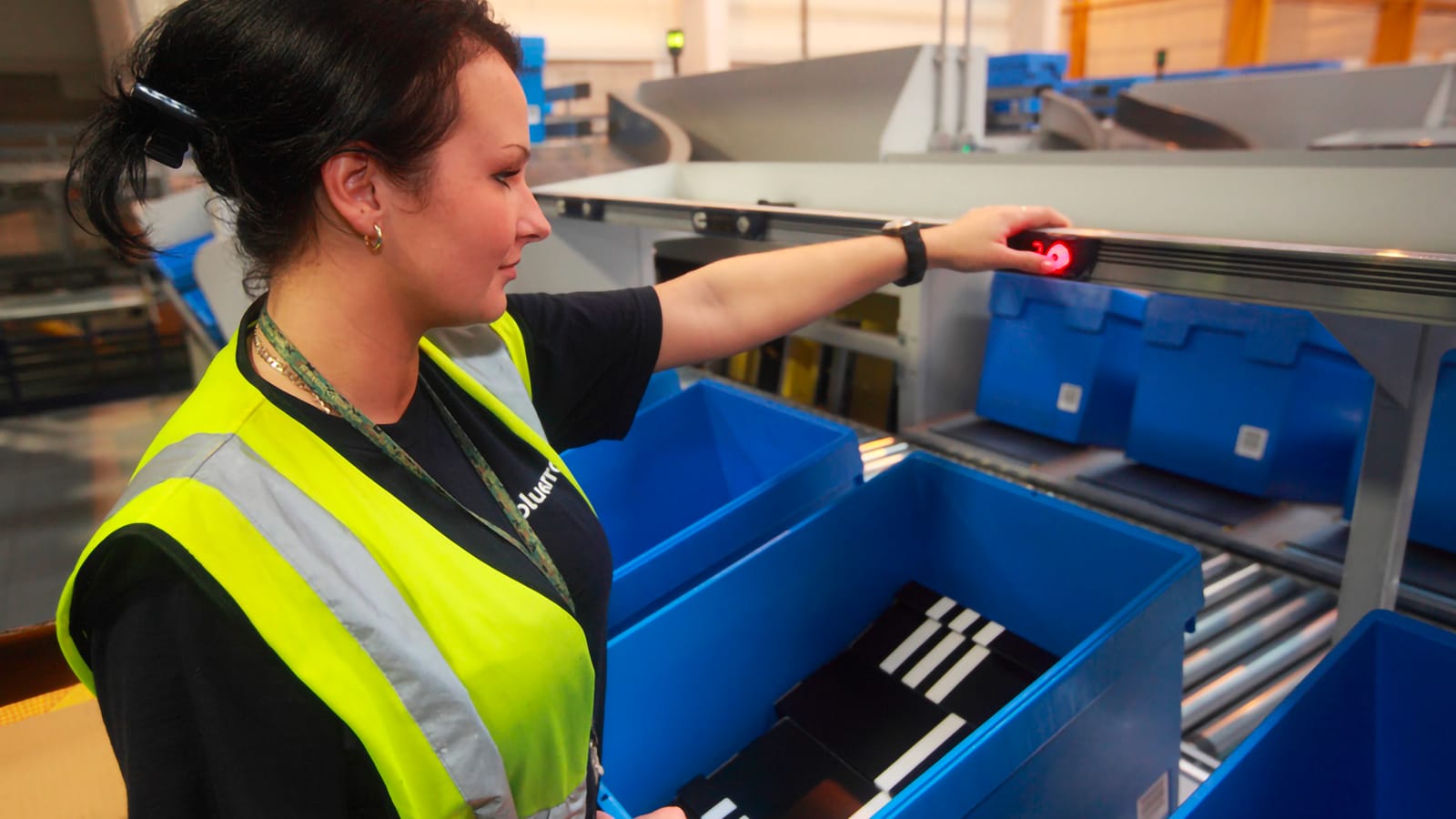
Die globale Sportbekleidungsmarke Adidas stand vor großen Herausforderungen bei der Bewältigung des schnellen Wachstums und der gleichzeitigen Konsolidierung der Geschäfte in Nordeuropa. Die Zusammenarbeit mit Dematic und die umsichtige Investition in die Auftragsdistribution erwies sich als Gewinnstrategie.
Die Herausforderung
Die effiziente und pünktliche Distribution seiner hochmodernen Sportschuhe, Bekleidung und Accessoires ist für Adidas von entscheidender Bedeutung. Die Lieferkette wurde in den letzten Jahren durch die schnelle Expansion des Unternehmens auf die Probe gestellt.
Im Jahr 2006 stellte die Übernahme der Marke Reebok sowohl eine Herausforderung als auch eine Gelegenheit dar, den Vertrieb in der European Area North, der Einzelhändler im Vereinigten Königreich, Irland und den Benelux-Ländern beliefert, neu zu definieren und umzustrukturieren.
Die Analyse eines fusionierten Vertriebsnetzes machte deutlich, welche Effizienzsteigerungen durch die Konsolidierung der Bestände der fünf wichtigsten Marken adidas, Reebok, TaylorMade, Rockport und Ashworth erzielt werden können. Vier bestehende konventionelle Lager mussten durch eine einzige automatisierte Distributionsanlage in Trafford, Manchester, ersetzt werden.
Neue Kommissionierungsstrategien für New Trafford
Das speziell gebaute 32.500 Quadratmeter große DC in Manchester wurde innerhalb von 18 Monaten fertiggestellt. In Zusammenarbeit mit Adidas hat Dematic ein dynamisches, platz- und kosteneffizientes Lager geschaffen.
Das integrierte Design umfasst große automatische Lager- und Abrufsysteme (ASRS) für Paletten und Behälter sowie ein hocheffizientes Ware-zu-Mensch-Kommissioniersystem (GTP).
Dank der integrierten Hochdurchsatz-Einlegestationen kann der Bediener bzw. die Bedienerin bis zu 24 Aufträge gleichzeitig bearbeiten. Mit einer Kommissionierleistung von durchschnittlich 500 Einheiten/Stunde und einer Kapazität von bis zu 1500 Einheiten/Stunde kann Adidas nun mehr als 40.000 Split-Case-Teile pro Tag kommissionieren.
Tim Adams, Global Business Solutions Warehousing, adidas Group„Durch die Automatisierung können wir ein großes Volumen auf relativ kleinem Raum abwickeln, was die Gemeinkosten niedrig hält.“
Beseitigen von Kommissionierflächen und Auffüllung
Es stellte sich bald heraus, dass das System nicht nur die langsam drehenden Waren, sondern auch die große Mehrheit der Split-Case-Waren problemlos bewältigen konnte, so dass Adidas die für die manuelle Kommissionierung vorgesehene Fläche um zwei Drittel reduzieren konnte. „Bei über 70.000 Artikeln wäre die Kommissionierfläche für manuelle Vorgänge riesig gewesen, und angesichts der saisonalen Natur unseres Geschäfts hätten wir sie ständig ändern müssen – Automatisierung verbessert die Effizienz um das Dreifache“, so Tim Adams, Global Business Solutions Warehousing, adidas Group.
Platzeffiziente Lagerung
Das Großlager ist ein vollautomatisches Hochregallager mit 20.000 Palettenplätzen, das mit fünf Dematic-Palettenkränen ausgestattet ist. Palettierte Ladungen, die das Hochregal verlassen, sind entweder für den Versand bestimmt oder werden zu einer der vier Stationen für die Kommissionierung der Kartons gebracht.
Das vollautomatische Dematic-Miniload-Lager verfügt über mehr als 300.000 Stellplätze und wird von 12 Kränen angefahren, die jeweils mit einem doppelttiefen Lastaufnahmemittel ausgestattet sind, das vier unterschiedlich große Lasten gleichzeitig handhaben kann. Das System kann beeindruckende 800 Doppelzyklen pro Stunde durchführen.
Tim Adams, Global Business Solutions Warehousing, adidas Group„Automatisierung trägt zur Optimierung der Auslastung von Arbeitskräften und Ressourcen bei, indem sie Nachfragespitzen und -tiefs glättet.“
Automatisierte Kommissionierung von Behältern
Die Kisten werden von dem Dematic-Lagerverwaltungssystem „DC Director“ zu den Behälter-Umfüllstationen und dann weiter zu den Hochdurchsatz-Einlegestationen geleitet.
Jede der vier Hochdurchsatz-Einlegestationen verfügt über 24 Einlegeplätze für Kundenaufträge, so dass bis zu 24 individuelle Aufträge gleichzeitig bearbeitet werden können. Das Miniload-System und das integrierte Fördersystem sorgen für einen reibungslosen Fluss der Artikel zum Kommissionierer bzw. der Kommissioniererin, und zwar genau in der für die Auftragserfüllung benötigten Reihenfolge. Wenn die Behälter oder Kartons an den Kommissionierstationen ankommen, werden sie in eine für den Bediener bzw. die Bedienerin vorbereitete Position gehoben.
Betrieb mit Hochdurchsatz-Einlegestationen
Auf einem Bildschirm werden Anweisungen mit einem „Putto-Light“-System für jeden Auftragsort angezeigt, das angibt, in welchen der 24 Auftragsbehälter die Artikel gelegt werden sollen.
Abgeschlossene Aufträge werden auf ein Mitnahmeband geschoben und zu den Packstationen transportiert oder, im Falle von teilweise abgeschlossenen Aufträgen, in einen automatischen Puffer geschickt, bis der Auftrag abgeschlossen ist.
Um die Genauigkeit zu gewährleisten, wird jeder Split-Case-Artikel gescannt, bevor er an einer der 22 Packstationen des DC in einen Versandkarton gepackt wird.
Steuerung des Lagers
Die Steuerung der automatisierten Anlage erfolgt über die Dematic-iQ-Software, die mit dem Manhattan-Associates-WMS von Adidas integriert ist.
„Dematic iQ ist viel einfacher zu bedienen als andere Systeme, die ich gesehen habe“, sagt Stuart Jones, Project Manager, Global Warehousing bei der adidas Group. „Das Software-Team von Dematic war sehr zuvorkommend, unkompliziert in der Zusammenarbeit und sehr einfallsreich, um das Beste aus dem System herauszuholen.“
Fazit
Die Vorteile, die sich aus dieser 20 Millionen Pfund schweren Investition in die Automatisierung ergeben haben, prägen nun die Art und Weise, wie Adidas seine Vertriebsstrategie für Europa und weitere Märkte betrachtet.
Adidas hat erlebt, wie Automatisierung viel flexibler geworden ist. Eine Reihe neuer Möglichkeiten sind entstanden – von der Kommissionierung von Kartons bis hin zu einem einzelnen Paar Schuhe – was eine viel größere Genauigkeit ermöglicht hat.
DC-Statistiken
- Größe der Anlage: 32.500 Quadratmeter
- Palettenlager: 20.000 Plätze
- Miniload-Lager: 300.000 Plätze
- Stock Keeping Units: 70.000+
- Packstationen: 22