Spezialisierte Lösung für die automatisierte Kommissionierung von frischem Obst und Gemüse
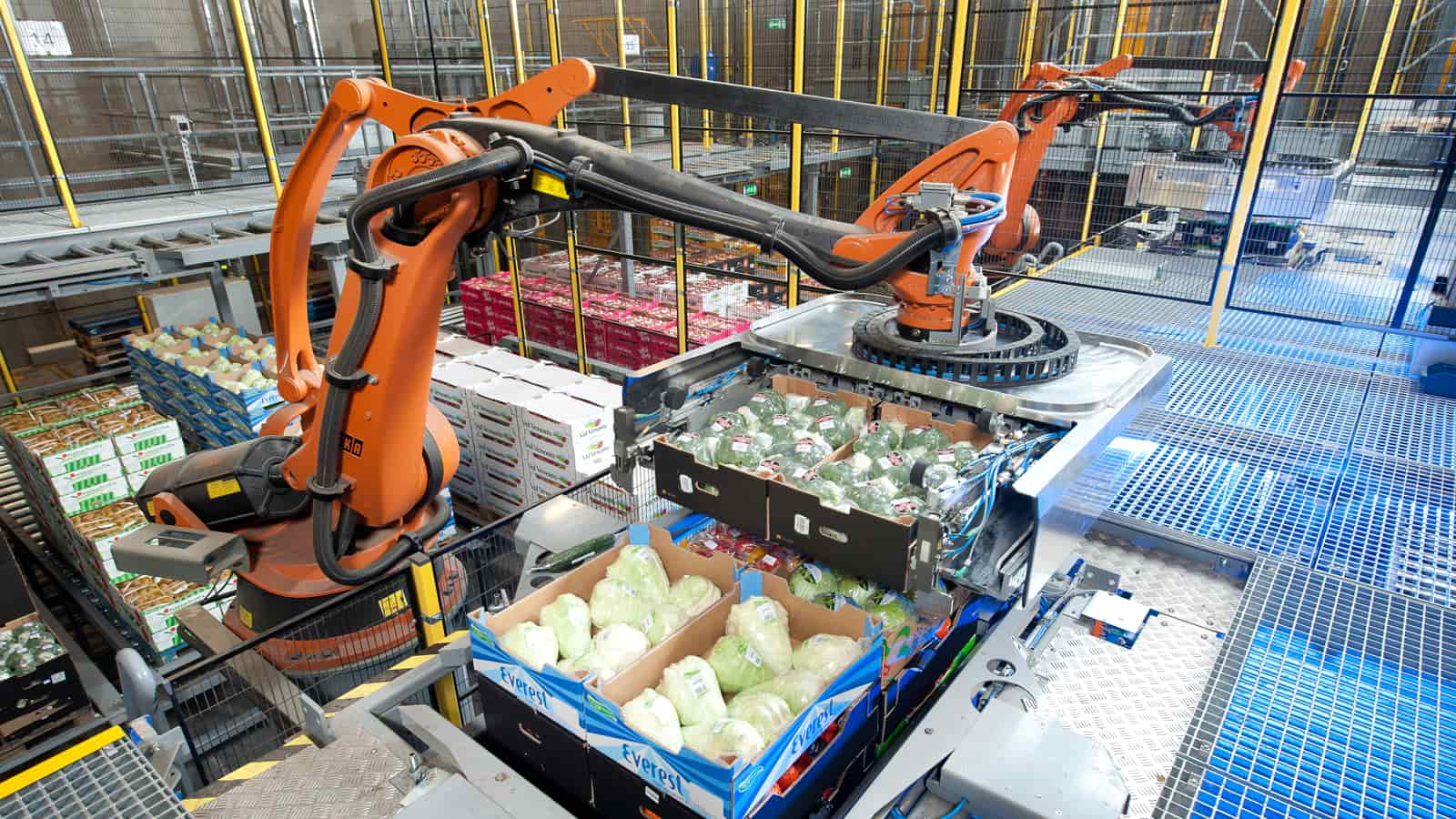
Netto – Køge, Dänemark – Dematic hat für die dänische Supermarktkette Netto eine einzigartige Systemkonzeption integriert, in der völlig neu entwickelte Logistiktechnologiekomponenten und Hochleistungsroboter für die automatisierte, filialbezogene Palettierung von Kisten und Kartons mit Obst und Gemüse zum Einsatz kommen: Auf diese Weise werden ein warenschonendes One-Touch-Handling, eine gesteigerte Produktivität und eine schnelle Amortisierung erreicht. Die innovative Konzeption schafft eine spezialisierte Lösung für den automatisierten Frischwarenumschlag.
Auftragsstruktur
Für das zentrale Distributionszentrum von Netto im dänischen Køge, etwa 40 km südlich von Kopenhagen, hat Dematic eine innovative Lösung für die automatische Kommissionierung und Palettierung von Obst und Gemüse implementiert. Mehr als 70 % der Auftragspaletten werden mit der neuen Lösung im zentralen Frischwaren-Umschlagslager der dänischen Supermarktkette nun vollautomatisch kommissioniert.
Als Generalunternehmer hat Dematic das neue Netto-Lager mit technologischen Innovationen (basierend auf der neuesten Robotertechnologie und neuen Materialflusskomponenten) und mit einer integrierten, intelligenten Materialflusssteuerung ausgerüstet.
Leistungs- und Lieferumfang:
- Integration von Hochleistungs-Palettierrobotern mit speziellen Greifersystemen für das voll automatisierte Kommissionieren und Verpacken von Paletten
- Förderanlagen
- Bereich für die manuelle Pick-by-Voice-Kommissionierung
- Dematic iQ Software
- Servicevertrag
Die Herausforderung
Bereits bei der Errichtung der Distributionszentren im Jahr 2003 hatte Netto nach einer Lösung gesucht, die mit minimalem Handling der Ware einen hohen Durchsatz und Automatisierungsgrad ermöglichte.
Im Frischesegment des Lebensmittelhandels gelten eine effiziente Supply Chain und ein One-Touch-Handling als oberste Devise. Anforderungen der dänischen Arbeitsschutzbehörde in Bezug auf das täglichen Heben von Lasten haben dieses Projekt angestoßen. Das Konzept stellt besondere Herausforderungen an die Intralogistik. Das liegt daran, dass eine Automatisierung der Prozesse (eine bewährte Methode für das Handling von Kisten/Kartons) angesichts der Empfindlichkeit der Waren nicht praktikabel war.
Ziele
- Höhere Leistung und höherer Durchsatz
- Automatisiertes Handling von Frischwaren
- Schnelle, optimierte Handlingprozesse
- Schneller Umschlag
- Einhaltung örtlicher Sicherheitsvorschriften
Technische Daten
- 15 Palettierroboterzellen
- Handling von Kartons, Steigen und Kisten
- Gleichzeitige Kommissionierung von 75 Produktgruppen
- Bis zu 28 verschiedene Kolli pro Palette
- Roboterpicks/Tag: ca. 75 SKUs
- Manuelle Picks/Tag: ca. 50 SKUs
- Zeit für die Auftragsbearbeitung: weniger als 30 Minuten
Die Lösung
Das zentrale Frischwaren-Umschlagzentrum von Netto ist eines der technologisch fortschrittlichsten Logistikzentren in Dänemark. Gleichzeitig gilt in Dänemark eines der strengsten Arbeitsschutzgesetze. Dieses regelt unter anderem, wie viel Gewicht ein Mitarbeiterinnen und Mitarbeiter pro Schicht insgesamt heben und bis zu welcher Höhe der Zugriff auf die Waren erfolgen darf. Deshalb kommen in dänischen Logistikzentren häufig Scherenhubtische zum Heben und Absenken von Paletten zum Einsatz. Das bedeutet, dass es gerade in Bezug auf das Handling von Obst und Gemüse schwierig war, etwas zu ändern. Die empfindlichen Waren mussten manuell verpackt werden.
Mit der neuen integrierten Lösung von Dematic ist das jedoch anders. Dematic hat den Warenfluss zunächst auf drei Arten von Transportbehältnissen ausgelegt:
- Bananenkisten
- Obst- und Gemüsesteigen aus Kunststoff
- Kartons mit dem Grundmaß 600 x 400 mm
- Alle werden täglich auf bis zu 2,30 Meter hoch beladenen Paletten im Frischwaren-Umschlagzentrum Køge angeliefert. In Zusammenarbeit zwischen dem bei Netto eingesetzten Warehouse Management System (WMS) und dem von Dematic als Schnittstelle installierten Warehouse Control System (WCS) werden den Lieferanten spezifische Ladetore zugewiesen. Nach dem Andocken werden die Wareneingangspaletten auf einen Rollenförderer oder zur Bereitstellung in den manuellen Pick-by-Voice-Kommissionierbereich überführt.
Implementierung
Die Förderanlage verteilt die Wareneingangspaletten auf eine Förderstrecke. Diese beginnt mit vier Zuführpunkten, von denen aus die Paletten zu einer der Roboterzellen geleitet werden. Die Förderbahnen dienen als Zuführ- und als Rückführstrecke und werden jeweils nur mit artikelreinen Paletten bestückt. In der Zelle arbeiten Palettier-/Depalettierroboter. Von den auf der einen Seite der Zelle zugeführten Wareneingangspaletten nehmen die Roboter je nach den Einstellungen des IT-Systems ein oder zwei der Transportbehältnisse auf. In einem Arbeitsgang nimmt der Roboter also eine viertel oder halbe Lage der Palette auf und kommissioniert sie auf Auftragspaletten.
Dabei gibt das WCS von Dematic Beschränkungen für die Palettenbildung beispielsweise nach Gewicht und optimaler Volumennutzung vor. Für die erforderlichen Leerpaletten wurde ein separater Leerpaletten-Umlauf installiert. Dieser Pool besteht weitgehend aus den geleerten Wareneingangspaletten, die von den Robotern auf den Umlauf gesetzt beziehungsweise von ihm abgenommen werden. Hierfür sind die Greifer mit einem integrierten Palettenheber ausgestattet.
In Køge sind 15 solcher Roboterzellen eingerichtet, sodass gleichzeitig 75 verschiedene Produktgruppen kommissioniert werden können. Dank der Pufferkapazität an jeder Bahn wurden keine Umläufe oder Staustrecken für eine Sequenzierung benötigt. Das bedeutet, dass die Aufträge in den hintereinander positionierten Roboterzellen in Batches kommissioniert werden können. Das Palettenregal läuft die erforderlichen Roboterzellen nacheinander an.
Paletten werden immer mit höchstens 28 verschiedenen Kolli beladen – im ungünstigsten Fall bedeutet das zwischen Leerpalette und auftragsfertiger Versandpalette vier Stopps an den Roboterzellen. Die neu entwickelte, einzigartige Greiferkopftechnologie ermöglicht das Handling der drei wichtigsten Transportbehältnisse in allen 15 Roboterzellen, wobei für Redundanz gesorgt wird, indem Schnelldreher in mehr Roboterzellen platziert werden.
Das WCS steuert die Warenanlieferungen und die Filialpalettierung in den 15 Roboterzellen und optimiert den Verlauf über die Förderstrecke.
Die in den Roboterzellen automatisch kommissionierten Filialpaletten werden schließlich in den Palettenstapelhilfen über eine der beiden angetriebenen, mehrfach miteinander verbundenen Rollenbahnen selbstständig in Richtung Warenausgangsfertigung abgezogen. Dabei dient die doppelbahnige Förderstrecke sowohl zum Be- als auch zum Entladen der Roboterzellen. Die geleerten Wareneingangspaletten werden von den Roboterarmen aufgenommen und zur Weiternutzung an die Leerpalettenförderstrecke übergeben.
Das letzte Highlight der innovativen Anlagenkonzeption ist die Warenausgangsabfertigung. Diese befindet sich auf der zweiten Ebene. Hier werden die kommissionierten Filialpaletten in ihren Palettenstapelhilfen auf den Rollenbahnen zugeführt. In einer genauen, vorgegebenen Position unterhalb der Warenausgangsabfertigung schiebt der Lift die Filialpaletten von unten aus den Palettenstapelhilfen auf die zweite Ebene. Dies geschieht unter genau einem Wrapper.
Während die Palette angehoben und aus der Palettenstapelhilfe herausgeschoben wird, beginnt automatisch die Umwicklung der Palette mit Stretchfolie – von ihrem oberen Ende nach unten. Anschließend wird die fertig umwickelte, transportgesicherte Palette an den Warenausgangsbereich ausgesteuert.
Innovation
Zwei weitere Merkmale sind bei dieser außergewöhnlichen Anlagenkonzeption von Bedeutung:
- Der neu entwickelte Kombi-Greifer der Roboter
- Eine speziell entwickelte Palettenstapel- und Transporthilfe
Das Greifersystem ist eine Innovation. Zum einen werden hiermit die Leerpaletten bewegt. Zum anderen ist es mit seinen pneumatischen und mechanischen Vorrichtungen speziell auf das Handling der drei wichtigsten Transportbehältnisse für die sensiblen Obst- und Gemüse-Anlieferungen ausgelegt: Je nach Anforderung können die innovativen Greifer Kartons und Kisten von oben, von unten oder durch seitlichen Druck aufnehmen. Dies ist eine bislang einmalige Anlagenkonzeption. Die zweite wichtige Innovation ist die speziell für dieses Konzept entwickelte Palettenstapelhilfe. Sie dient sowohl zur Unterstützung einer stabilen Palettenbildung als auch als Transportbehälter für den automatischen innerbetrieblichen Warenfluss. Für die Palettenstapelhilfe, die die Auftragspaletten bei der Kommissionierung umschließt, ist unterhalb des Palettierbereichs eine separate doppelbahnige Förderstrecke eingerichtet. Sie wird an einer im Roboterzellenlayout exakt definierten Position gegenüber den Wareneingangsbahnen positioniert. Hier hält ein Liftsystem die Paletten bei der Beladung durch die Robotergreifer für jede Ebene auf gleicher Höhe und senkt diese sukzessive ab, bis die Auftragspaletten fertig kommissioniert sind.
Ergebnis
Seit Übergabe der Anlage werden in Køge täglich 2.700 Auftragspaletten mit Obst und Gemüse für die Belieferung von 275 Filialen zusammengestellt. Die innovative, integrierte Lösung von Dematic verringert die Bearbeitungszeit für Obst und Gemüse, sodass ein Auftrag in weniger als 30 Minuten erledigt werden kann.
Bis zu 50 weitere SKUs werden von den Mitarbeiterinnen und Mitarbeiter im Bereich der manuellen Kommissionierung bearbeitet und durch Auftragspaletten vervollständigt oder die Auftragsabfertigung wird durch Zuführung einzelner Kolli abgeschlossen. Für den manuellen Kommissionierbereich hat Dematic eine Pick-by-Voice-Lösung bereitgestellt. Diese beinhaltet die gesamte Kommunikationsstruktur und die Anbindung an das WMS sowie – neben der IT-Hardware wie den Applikations- und Datenbankservern – die Ausstattung für das operative Handling mit Headsets, Scannern, Funkdatenterminals und PCs.
Ein weiterer Erfolgsfaktor der Lösung ist die Software. Die komplexen Betriebsabläufe lassen sich auf diese Weise nur durch die Vielzahl der von der Software angewandten Algorithmen optimieren.
So umfasst das IT-System von Dematic nicht nur eine optimale Bereitstellung mit minimalem Aufwand für die filialgerechte Kommissionierung sowie gespeicherte Einstellungen für eine sichere und stabile Palettenzusammenstellung. Die Software übernimmt auch das automatische Leerpalettenmanagement, ermittelt in Echtzeit unter anderem die Prioritäten für die Auftragsabfertigung, sorgt für einen optimalen Lastausgleich zwischen automatisierter und manueller Kommissionierung nach Auftragsprofil oder versorgt die Etikettenstationen an den Stretchern mit den nötigen Informationen für den Etikettendruck.
Mit bewährten, wartungsarmen Fördertechnikkomponenten, modernsten Technologien für automatisierte Prozesse und einem leistungsstarken, auf alle Anforderungen ausgelegten IT-System sowie einem Zweijahres-Servicevertrag ist die Netto-Anlage bereit für die Zukunft.
Abgesehen von den schnellen, optimierten Handlingprozessen profitiert Netto durch die Anlagenkonzeption von Dematic von zusätzlichen Freiflächen für die Versandvorbereitung sowie von Möglichkeiten für weitere Wareneingangs- und Durchsatzsteigerungen. Mit der jetzt in Køge installierten Anlage hat Dematic ein umfassendes Gesamtkonzept für die automatisierte Kommissionierung filialgerecht zusammengestellter Obst- und Gemüsesortimente umgesetzt, das weltweit einzigartig sein dürfte.
Vorteile für Kundinnen und Kunden
- Auftragspaletten mit Obst und Gemüse werden täglich automatisch für die Belieferung der Filialen zusammengestellt
- Etwa 75 SKUs werden täglich in den Roboterzellen verarbeitet
- Etwa 50 SKUs werden täglich von Mitarbeiterinnen und Mitarbeitern in der manuellen Kommissionierung abgefertigt
- Integrierte Lösung für die automatisierte, prioritätsgeführte Palettenbildung
- Optimale Gewichts- und Volumennutzung durch Dematic WCS-Spezifikationen für die Palettenbildung
- Auftragsbearbeitung in weniger als 30 Minuten
- Die kompakte Anlagenkonzeption bietet zusätzliche Freiflächen für die Versandvorbereitung und erlaubt Optionen für weitere Wareneingangs- und Durchsatzsteigerungen
- Konzeption, Lieferung der Komponenten, Neuentwicklungen und IT aus einer Hand
- Zweijahres-Servicevertrag
- Ergonomisches Design entsprechend den dänischen Sicherheitsvorschriften