The Temperature Controlled Warehouse
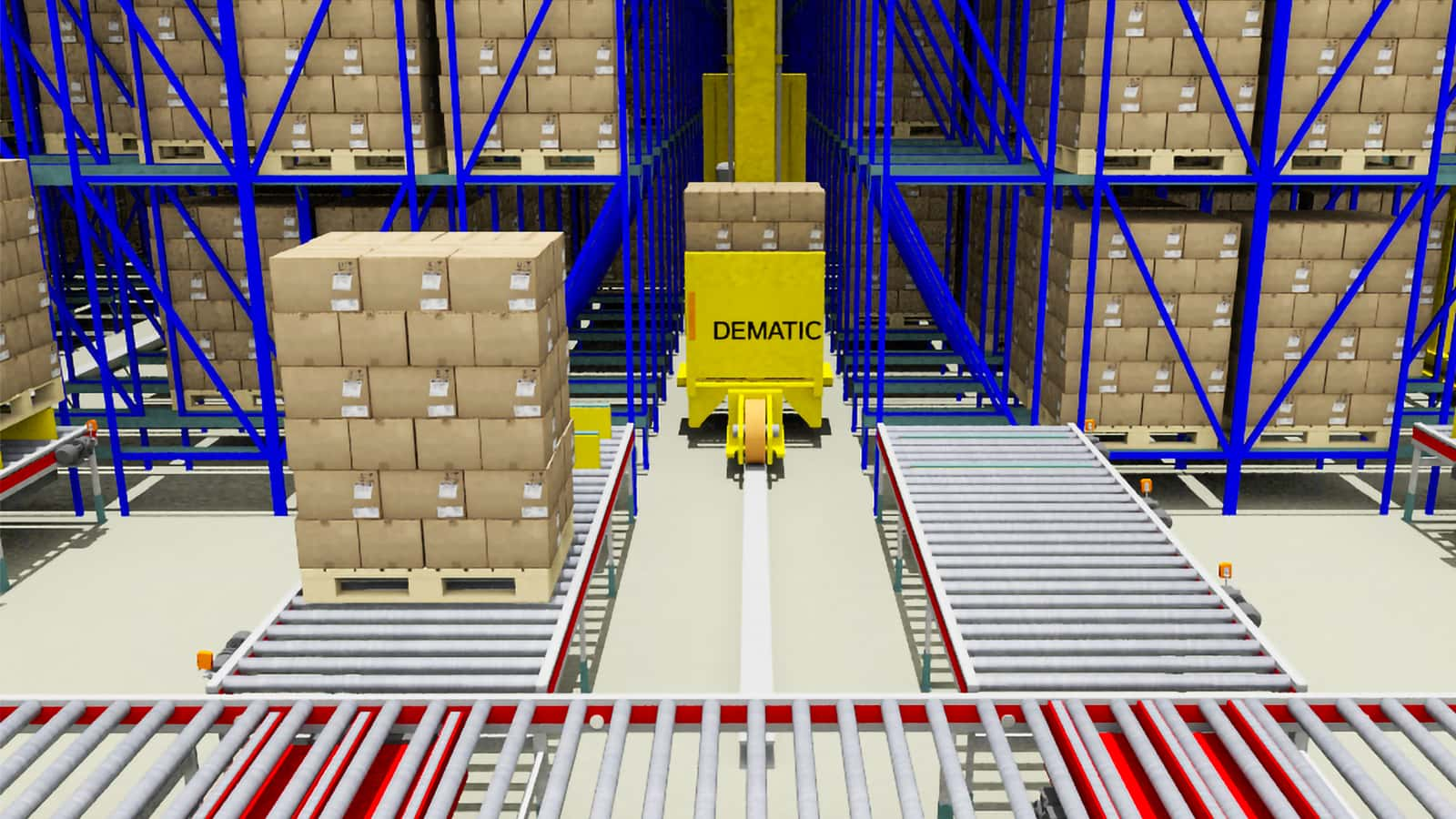
Automated Versus Traditional
The business case for automating the temperature controlled warehouse, either freezer or cooler, is stronger than ever. More food and beverage distribution operations are reconsidering their existing traditional warehouse designs. As compared to a traditional temperature controlled warehouse, here are the key benefits of more automation:
Smaller Building Footprint – Because an automated warehouse features a high bay configuration, a smaller building footprint is required. The smaller building footprint is typically 25% of a traditional warehouse.
Reduced Cubic Space – Since the automated warehouse utilises a high density configuration, less cubic space is required for the same amount storage. This reduction is approximately 25% to 35%.
Tax Advantage – The construction for an automated building typically includes a rack supported building. Unlike the rack with a traditional warehouse, the rack supported building has a tax advantage. (It can be depreciated as machinery, which has a more favourable tax structure.)
Energy Savings – The energy operating costs are reduced with the high density configuration of the automated warehouse (more storage in less refrigerated space). Energy costs for cooling are higher than heating. Most loss is from the roof. AS/RS has smaller roof surface. Energy savings range from 35% to 50% less with automated warehouse. (Note: Energy prices are likely to continue to rise.)
Improved Freezer in/out Control – The doors to the automated freezer warehouse are smaller and are open less thereby providing additional operational efficiency through energy savings.
Minimised Exposure to Harsh Environment – Workers are not required in the automated freezer warehouse. Instead, order fulfilment and load consolidation occurs on the shipping/receiving dock in ambient temperatures. Elimination of labour in the harsh freezer environment means improved worker ergonomics, improved labour productivity, and the end of worker recruitment issues related to filling staff positions that require work in a freezer. Employee turnover rates for freezer environment position tends to be high.
Less Defrosting – Traditional warehouse defrosts once per day, automated warehouse defrosts once per week. This translates to energy savings.
Reduced Damage – Since the automated warehouse does not require manually operated fork lift trucks, damage to racks, product, freezer doors, and the facility can be eliminated. (Rack damage is costly to repair.) On average, a traditional freezer warehouse may need to replace a freezer door once per month due to fork truck damage.
Control of Downtime – In a traditional warehouse, if employees are not available, the operation is down. If technology is down, managers have direct control to bring the technology back up.
Increased Safety – No people are permitted in the aisles of the automated warehouse, thus eliminating safety issues. In traditional warehouses, manually operated fork lift trucks create safety risks.
Improved Inventory Accuracy – Accurate computer control of inventory location in the automated warehouse eliminates location errors that occur with the manual fork truck method of inventory put-away. (With the traditional warehouse, inventory can at times become temporarily “lost” in the warehouse.) Furthermore, inventory accuracy translates to a selling feature for freezer warehouse operations that solicit 3PL contracts. Prospective 3PL customers are favourably impressed with service providers that deploy technology that can provide extremely high inventory accuracy.
Omit Physical Inventory Counting – With the automated warehouse, taking physical inventory counts is not required. This reduces operational costs.
Improved Order Accuracy – The overall benefit of accurate inventory location in the warehouse and FIFO inventory rotation, is improved order accuracy. Furthermore, the cost of an inaccurate order for a food distributor is significant. When a customer needs a food product, that customer needs it the day of delivery. If an inaccurate order is delivered to a customer, a costly emergency expedited delivery is required to satisfy the customer (including the corrected shipment at some later date is not an option, the customer needs the product that day). The cost to fix an incorrect order range from $100 to $500 on average. Traditional warehouses can experience several picking errors per day. Automated systems may experience a picking error once per month.
High Order Fulfilment Rate – Due to the high inventory accuracy with the automated warehouse, order fulfilment rates (ability to fill orders) is approaching 100%.
Weigh Check Adds Accuracy – Automated systems typically include inline, automated weigh scales. These scales verify weight of loads thereby capturing a potential accuracy problem.
FIFO Rotation – With computer control of inventory in the automated warehouse, product freshness is assured by rotating stock FIFO. This greatly reduces issues with expired products. With the traditional warehouse, fork truck drivers may not always pick the oldest inventory first when performing order fulfilment tasks.
Control of “Quarantined” Product – With the automated system, inventory that is quarantined is electronically locked in.
Improved Product Integrity – With the automated system, the pallets are optimally spaced such that freezer air can circulate adequately thereby insuring quality freezer storage.
Improved Service Reputation – Customers expect accurate orders once the trend has been established, Customers are less likely to first blame the distributor for an error since order accuracy is so high. Most of the time, customers find the mistake is actually at their end.
Forces Operations Discipline – An automated system forces system discipline such that there is little chance to place product in the wrong place.