Lion Beer Australia Deploys Dematic AGVs
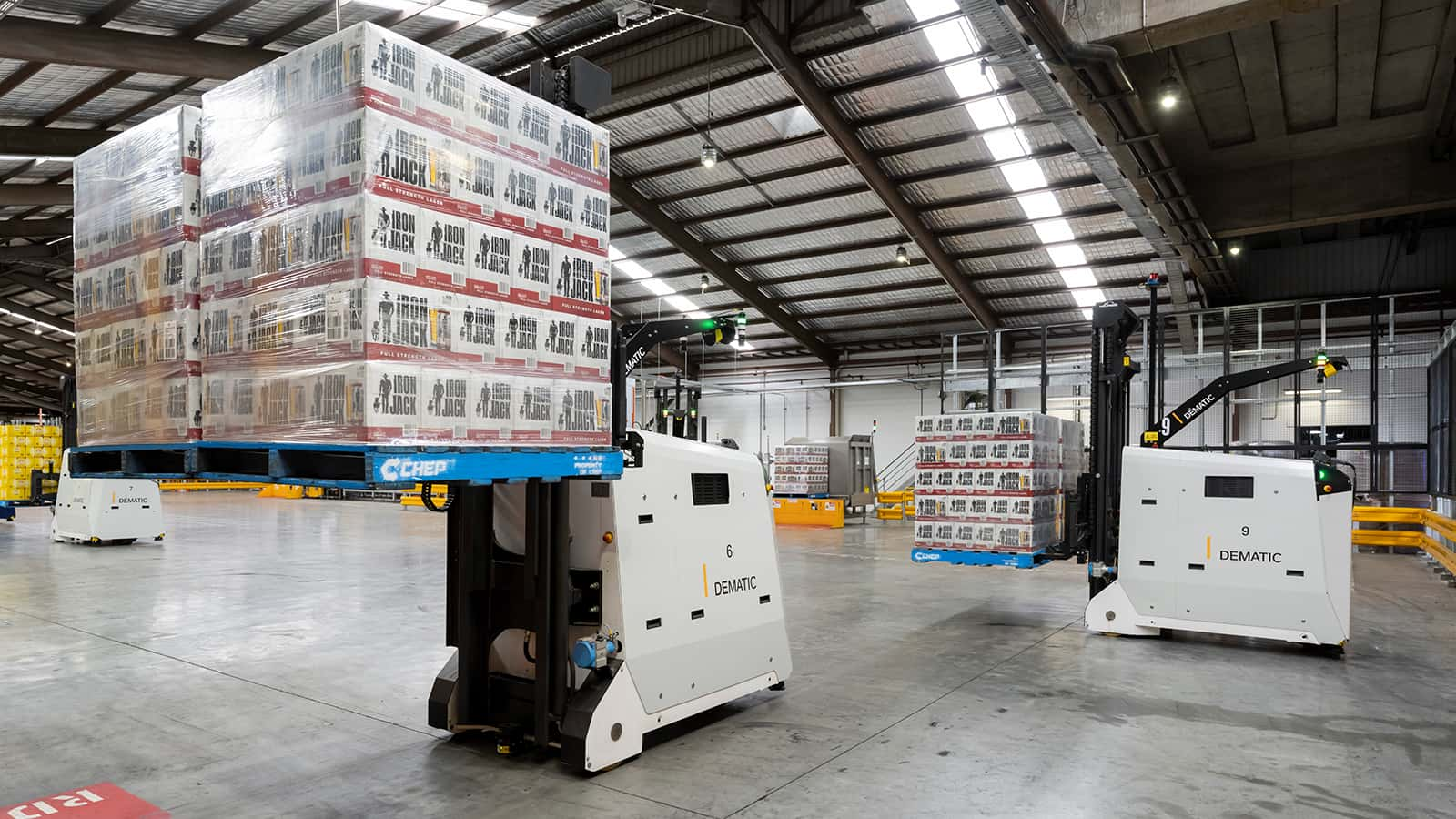
Tim Symons, Packaging Manager at TooheysWe needed a definitive way to improve our productivity to keep up with demand, whilst also remaining cost-effective and competitive within the market.
Lion is one of Australasia’s largest beverage companies, employing over 4,000 people across Australia and New Zealand. Lion markets premium brands in the beer, cider, fine wine, spirits and both alcoholic and non-alcoholic ready-to-drink beverages. With this diverse portfolio, Lion collectively generates a revenue of around AUD$3.958 billion each year.
Lion, a subsidiary of Kirin Holdings, is a company focused on long-term, sustainable growth. Its business strategy runs alongside maintaining an efficient balance between production and distribution and focuses on expanding in home and venturing into new markets, while always keeping the consumer and customer at the heart of all operations.
With a total of 15 key beer brands featuring Tooheys, XXXX, Hahn, and James Squire, the diversification of the category led Lion to initiate a new program of innovation and automation to improve production efficiency and streamline operations at its largest facility, the Tooheys Brewery in Lidcombe, New South Wales, Australia.
The Tooheys Brewery operates 24 hours a day, seven days a week, and brews up to 300 million litres of beer per year and produces up to 120,000 cartons of product per day, which is equivalent to 2 million litres per day.
Lion’s shift to an automated, future-proof supply chain
Following significant growth in its product range, Lion initiated a re-structure of its supply chain and internal fulfilment operations in an effort to future-proof its manufacturing and supply chain operations to maintain competitiveness and resilience. With the market dynamics pushing the beverages supply chain into a 24/7 cycle, it was clear that Lion’s previous legacy systems were outdated and in need of upgrading. Lion’s overarching goal was to make upgrades that would help the company meet the needs of its consumers whilst also looking after its own employees by providing a safe and well-managed workplace.
As part of the upgrade project, the decision was made to implement Automated Guided Vehicles (AGVs) from Dematic, an intralogistics innovator that designs, builds and supports intelligent, automated solutions for retail, manufacturing and distribution operations.
Tim Symons, Packaging Manager at Tooheys, said the implementation of AGVs was part of a widespread initiative to streamline operations within the Tooheys Brewery and across the entire business.
“We needed a definitive way to improve our productivity to keep up with demand, whilst also remaining cost-effective and competitive within the market,” said Tim.
“To achieve this, we invested in AGV technology as a way to better deliver services to our core assets – our people, brands, production facilities and suppliers - and to generate better value for our customers.”
A solution to automate and streamline operations
Lion selected Dematic as its automation partner due to its track record of successfully implementing automated solutions to manufacturing and distribution operations, as well as its global expertise in supply chain optimisation.
The Dematic AGVs were selected as the ideal solution to be deployed at Lion’s Tooheys Brewery in Lidcombe because they were capable of operating with reliability and consistency - eliminating all possible traffic blockages between the automatic palletiser and despatch, even when all palletising lines are running simultaneously, working to keep product moving regularly within the entire facility.
“Our old system was extremely manual, which made it less reliable and prone to frequent breakdowns which would interrupt the entire production facility. Additionally, the reliance on forklift drivers and warehouse worker interactions created a large safety risk. If you combine this with the general inefficiencies of manual forklift operations and the frequent level of maintenance needed to run them, this system was simply not futureproof, and so, our decision to move to automation was necessary,” said Tim.
AGVs work to manage and automate all activity within the warehouse that would otherwise be operated by manual machinery such as a forklift; working to connect both outbound and inbound products with automated truck loading. The AGV’s high-precision navigation of the warehouse floor, combined with its dexterous design allows it to utilise any warehouse space, eliminating the need for extensive use of pallet conveyors. With a smaller turning circle than a forklift truck it can easily manoeuvre in tight spaces.
Tim Symons, Packaging Manager at TooheysA core objective for this project was to implement a new solution that eliminated human contact to products. Now, using AGVs, we don’t have any of our operators touching the products, or putting themselves in harm’s way by lifting and transporting heavy items and pallets.
“Likewise, we wanted the solution to help us optimise our supply chain to prepare it for the future. The reliability of AGVs has given us the confidence that the product that we, as a company, have nurtured through the brewing and production process is going to be a good fit for our customers at the end of the line.”
Using the AGVs increases reliability, with the AGVs capable of working non-stop 24/7 every day of the year. This is in addition to improving efficiency and accuracy of operations, thereby minimising mistakes, product damage and workplace accidents, which provides significant improvements in occupational health and safety standards.
“The major requirement for the Lion AGV solution was to operate at a faster rate than any palletisation activity done with a manual forklift, with the end result being to eliminate all manual activity completely,” said Tony Raggio, General Manager of Sales, AGVs, Dematic.
“The AGVs working at the Lidcombe facility are broken down into two distinct areas: zone one and zone two. The zone one AGVs work to handle full pallets from a robotic palletiser, which has the capacity to handle both twin pallets and single pallets. The AGVs are then brought over to the second zone, where the pallets are handled and moved on to a ‘roll on roll off conveyor’ and automatically loaded into the back of a truck,” said Tony.
AGV management systems controls the AGVs as well as interfaces with a company’s existing warehouse management system (WMS), to track product flow from production to storage and all the way through to despatch. AGVs can also be programmed remotely to carry out required tasks.
“The robust design of our AGVs means it can withstand the typically challenging environment of a warehouse, all whilst providing a 360° safety field of protection with automatic sensors to detect any obstruction. This enables it to co-work with operators and any other warehouse machinery or vehicles,” said Tony.
The AGV solution rollout
For the solution to be deployed successfully, it needed to be implemented into Tooheys Brewery’s high pace and fully operational manufacturing and supply chain environment. During the rollout process, Dematic worked closely with Lion and other partners working on-site, to allow Lion to continue producing the required rate of pallets of beer, whilst simultaneously integrating the AGVs.
The AGVs were successfully installed and commissioned whilst the site was still in full operation, allowing Lion to continue general operations to meet all product delivery commitments during this period. Additionally, Dematic collaborated with Lion to ensure the solution was tailored to and working effectively within the facility during this time.
“Through large amounts of coordination, we worked in collaboration with the Lion team and all other on-site partners contributing to implementation of the project. We had our highly experienced team on-site providing end-to-end management and support to ensure a successful rollout was achieved as quickly as possible,” said Tony.
Dematic had a team of in-house project managers, technicians, and AGV operators on-site throughout the implementation and testing phases of the AGV deployment project. Dematic also helped Lion to develop guidelines and work processes and procedures for staff.
“Dematic did a great job overseeing and managing the project and ensuring that the solution was deployed correctly in the facility. This gave us a really good insight into what the AGVs would look like in action and how they would navigate the warehouse floor and make the best use if its space,” said Tim.
Service and support
Through its full service and support program, Dematic will continue to help Lion on an ongoing basis to optimise system uptime, continuity of throughput and production efficiency. This will ensure Lion is getting the best ROI on its AGV investment.
“Our service and support program provides resources that ensure the best level of productivity is achieved. By working to reduce things like system downtime due to component failures, we can in turn reduce the overhead costs of system maintenance for Lion. The program offers assurance to Lion that the system has been supported in the best possible way, by us, the people who designed and built it,” said Tony.
Benefits of the new solution
For Lion, being able to invest in advanced automation technology such as AGVs to streamline warehouse operations and build a supply chain fit for the future has been a big achievement. This has allowed Lion to gain a competitive advantage in domestic and global markets.
“We are very happy with the progress and benefits we have already experienced using the AGVs in the warehouse. It has been an exciting process, and the possibilities are endless with this kind of automation, which has given us a really positive outlook towards how much better operations will run in the future,” said Tim. “This type of automation really ticks all the boxes for us, particularly in the way that it utilises the warehouse space so well and creates a much safer work environment for our staff.”
The AGV solution has supported Lion to construct a consistent measurement of product picking time, as well as eliminate any wastage, inaccuracies or mistakes made by human error throughout all phases of the picking process.
“The AGVs have helped give us real dependability for our end of the line process. By deploying Dematic’s AGVs, we are able to work within an area of operations that was once problematic – the transportation of pallets from palletising to despatch. With the AGVs, we know that they are reliable, and they have given us the confidence that our products are accurately and safely delivered to the end consumer with ease,” said Tim.
The AGV solution has also introduced a predictable logistics strategy. This allows Lion to gain insights into the number of vehicles in action within the warehouse, and how many pallets can be produced per day, per, shift, and per year – as opposed to a manual forklift environment which can create unpredictable outcomes such as injuries and staff availability.
Tony Raggio, General Manager of Sales, AGVs, DematicWith such a high level of autonomy, AGVs provide the backbone for a 24/7 operation to maximise service levels, which would otherwise be very costly to maintain. AGV systems can naturally grow with the addition of vehicles as volumes increase, and being exchangeable, they provide an unmatched level of system redundancy. As the human error factor is taken out of the equation, AGVs also eliminate costly product and equipment damage.
Warehouse operators have also experienced significant benefits and better worker satisfaction following deployment of the AGVs, due to the inherent efficiency, productivity, accuracy, quality control and safety benefits that can be gained in comparison to manual goods handling.
“A central goal for the AGVs was to create an all-round safer and more organised warehouse space. By implementing AGVs, the warehouse space is now quieter, lighter, and much more spacious, and it has allowed operators to focus more on their own key responsibilities while only interacting with the systems when they are having technical difficulties, rather than having to constantly operate machinery,” said Tim.
Future plans
Based on the successful implementation of the Dematic AGVs at the Tooheys Brewery in Lidcombe, and the operational benefits and improved throughput already achieved, Lion will look to deploy more AGVs at other breweries across Australia in the near future.