Specialised Solution for Automated Order Picking of Fresh Fruit & Vegetables
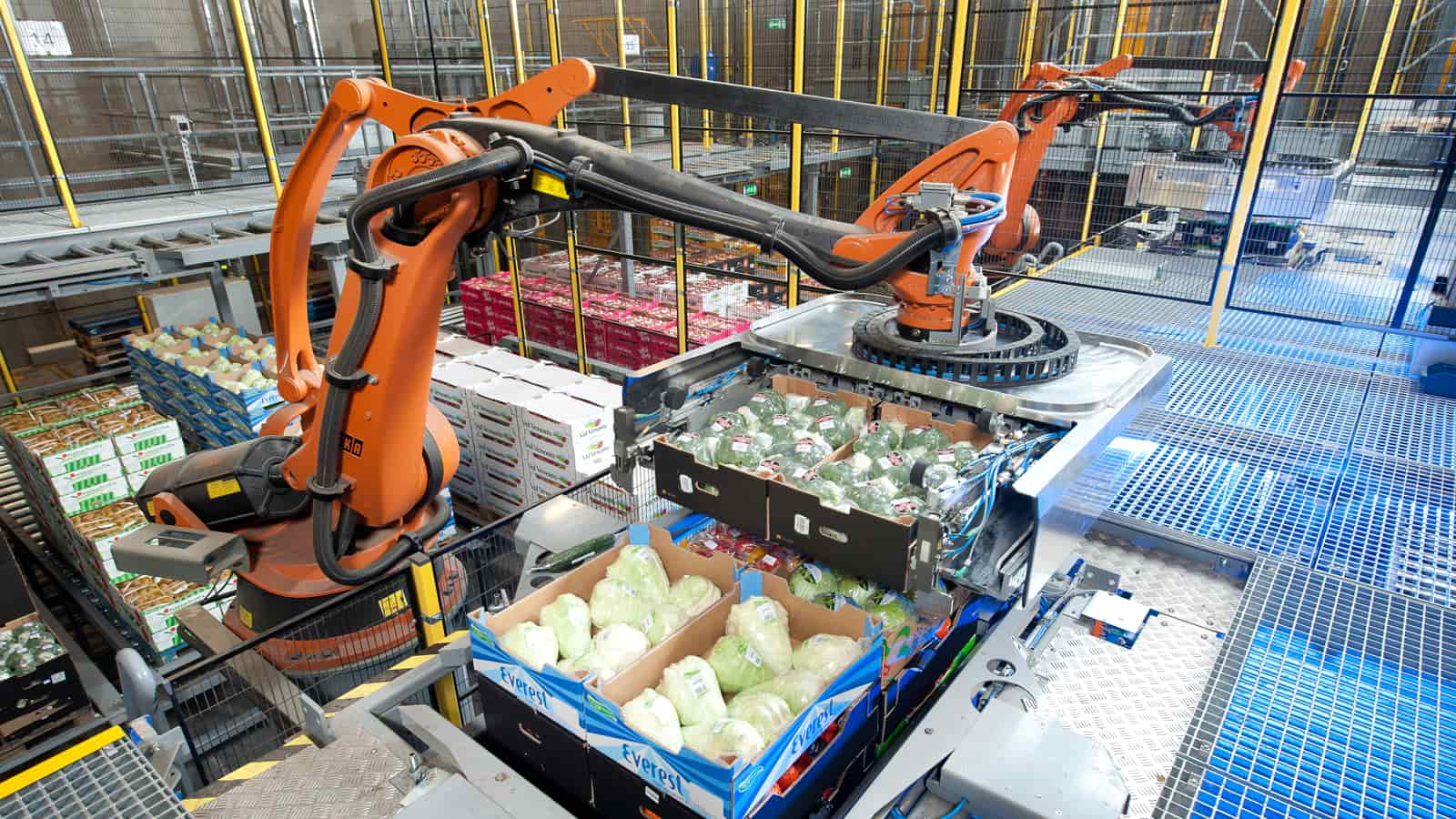
Netto – Køge, Denmark - For Danish supermarket chain Netto Dematic has integrated a unique system design using completely new developed logistics technology components and high-performance robots for automated, store-based palletisation of fruit and vegetable crates and cartons: One-touch handling that protects goods, produces high productivity, and provides rapid amortisation. The innovative design creates a specialist solution for automated fresh goods handling.
Order structure
For the central distribution centre of Netto, Dematic has implemented an innovative solution for automated order picking and palletising of fruit and vegetables in Køge, Denmark, around 20 miles south of Copenhagen. More than 70% of the order pallets are now picked and packed entirely automatically using the new solution in the central fresh goods handling warehouse for the Danish supermarket chain.
Dematic as general contractor equipped the new Netto warehouse with technological innovations (based on the latest robotic technology and new material flow components) and with integrated, intelligent material flow control.
Scope of service and supply:
- Integration of high-performance palletising robots with special gripper systems for fully automated pallet picking and packing
- Conveyor systems
- Manual Pick-by-Voice order picking area
- Dematic iQ software
- Resident service contract
The challenge
Since setting up the distribution centres in 2003, Netto had been looking for a solution, which with a minimum of goods handling permitted high levels of throughput and automation.
In the fresh goods sector of the food trade, an efficient supply chain and an one-touch handling are the primary objectives. Demands from the Danish working environment authority regarding daily lifting initiated the process of this project. The concept represents particular challenges to intralogistics. This is because process automation (a proven method of crate/carton handling) had not been feasible in light of the delicate nature of the goods.
Targets
- Higher performance and throughput
- Automated handling of fresh goods
- Fast, optimised handling processes
- Rapid turnaround
- Meeting local safety regulations
Technical data
- 15 robot palletising cells
- Handling or cartons, crates and boxes
- Picking of 75 product groups at the same time
- Up to 28 different packs per pallet
- Robot picks/day: approximately 75 SKUs
- Manual picks/day: approximately 50 SKUs
- Order processing time: less than 30 minutes
The solution
The central Netto fresh goods handling centre is one of the most technologically advanced logistics centres in Denmark. At the same time, Denmark has some of the strictest work safety regulations. These regulate, among other things, how much weight an employee can lift in total per shift, and up to what height goods can be accessed. Scissor lift tables used to raise and lower pallets are therefore a typical feature of Danish logistics centres. When handling fruit and vegetables in particular, this meant that it was hard to change anything. The delicate goods needs to be packed manually.
The new Dematic integrated solution is different, however. Dematic initially designed the goods flows for three types of handling units:
- Banana-boxes
- Fruit and vegetables in open plastic crates
- Carton boxes with base 600 x 400 mm
- All delivered on pallets loaded up to 2.30 meters high each day in the Køge fresh goods distribution centre. Specific loading gates are assigned to suppliers in collaboration between the Warehouse Management System (WMS) used at Netto and the Warehouse Control System (WCS) installed by Dematic as the interface. After docking, the incoming goods pallets are transferred to a roller conveyor or for allocation to the manual Pick-by-Voice order picking area.
Implementation
The conveyor system distributes the incoming goods pallets onto a conveyor line. It starts with four in-feed conveyor points that leads the pallets to one of the robot cells. The conveyor lanes are both feed and return paths and each lane only carries pallets of just one product. Pelletising/depalletising robots operates in the robot cell. When the goods pallets are fed into one side of the cell, the robots picks up one or two of the handlings units, according to the settings in the IT system. So in one operation, it’s a quarter or half pallet layer that the robot takes and puts them onto order pallets.
In this process, the Dematic WCS specifies restrictions for pallet formation such as weight and optimum volume utilisation. A separate empty pallet circulation system was installed for the required empty pallets. This pool consists largely of the empty incoming goods pallets positioned or removed by the robots on the circulation system. The grippers are equipped with an integrated pallet lifting device for this purpose.
There are 15 of these robot cells set up in Køge, meaning that 75 product groups can be picked at the same time. With buffer capacity at each lane there was no need for circulation or overflow paths for in-feed sequencing. This means that the orders can be picked in batches in the robot cells positioned one after the other. The pallet rack circulates to the required robot cells in sequence.
Pallets are always packed on the basis of a maximum of 28 different packs — in the worst case scenario, this means four stops between the empty pallet and completed shipping pallet to the robot cells. With the newly developed and unique gripper head technology, it’s possible to handle the three basic handling units on all 15 robot cells, with redundancy provided by placing fast movers on more robot cells.
The WCS controls the inward goods deliveries and the shop palletising on the 15 robot cells and gives an optimised route on the conveyor line.
The store pallets picked automatically in the robot cells are ultimately removed automatically in the pallet stacking guide systems via one of the two driven roller tracks connected at multiple points in the outgoing goods handling direction. In this process, the twin-track conveyor line is used both for loading and unloading the robot cells. The emptied incoming goods pallets are picked up by the robot arms and transferred to the empty pallet conveyor line for ongoing use.
The final highlight of the innovative system design is the outgoing goods handling system. This is located on the second level. Here the picked store pallets are fed in their pallet stacking guides on the roller tracks. In an exact, predefined position underneath the outgoing goods handling system, the lift pushes the store pallets from underneath out of the pallet stacking guides and onto the second level. This is carried out under precisely one wrapper.
To the extent that the pallet is raised and pushed out of the pallet stacking guide, the process of wrapping the pallet with stretch film begins automatically, from top to bottom. The fully wrapped pallet secured for transport is then directed to the outgoing goods area.
Innovation
Two other special features are important in this exceptional system design:
- The newly developed combi-gripper on the robots
- A specially developed pallet stacking and transport guide system
The gripper equipment is an innovation. First, it handles the empty pallets. Second, with its pneumatic and mechanical fittings, it is designed specifically for handling the three key handling units for the delicate fruit and vegetable deliveries: Depending on requirements, the innovative grippers can pick up cartons and crates from above, from below, or via sideways pressure. This is an one-off system design to date. The second key innovation is the pallet stacking guide system developed specially for this concept. It is used both to support stable pallet formation and for automatic internal goods flow as a transport container. The pallet stacking guide system holds the order pallets while picking, moving around on a twin-track, separate conveyor line installed underneath the palletising area. It is positioned at a precisely defined point in the robot cell layout in relation to the incoming goods lanes. Here, a lift systems holds and lowers the pallets successively when being loaded via the robot grippers at the same height for every level until the order pallets are completely picked.
Result
Since the handover of the system in Køge, 2,700 order pallets with fruit and vegetables are assembled for deliveries to around 275 stores each day. The innovative Dematic integrated solution reduces the processing time for fruit and vegetables so that order can be ready in less than 30 minutes.
A further maximum of approximately 50 SKU’s are handled by staff in the manual picking area, completed with order pallets or the order processing is finalised by the feeding in individual packs. For the manual picking area, Dematic has supplied a Pick-by-Voice solution providing the entire communication structure and connected to the WMS, and — in addition to the IT hardware such as the application and database servers — providing the equipment for operative handling with headsets, scanners, radio data terminals and PCs.
Another factor for the success of the solution is the software. The complex operative processes can only be optimised in this way via the range of algorithms used by the software.
The Dematic IT system covers more than just optimal provision with minimal effort for store-based picking or stored settings for safe and stable pallet assembly. The software also automatically handles empty pallet management, calculates the order processing priorities and more in real-time, provides the optimum load equalisation between automated and manual picking by order profile or supplies the label stations on the stretchers with the necessary label printing information.
Proven low-maintenance conveyor technology components, the latest technologies for automated processes and a powerful IT system designed to meet all requirements and a two year resident service contract make the Netto system prepared for the future.
In addition to the fast, optimised handling processes, the system design from Dematic has provided Netto with additional free space for dispatch preparation and also leaves options for further increases in incoming goods and throughput. With the system now installed in Køge, Dematic has implemented a comprehensive total concept for automated, store-based order picking of compiled ranges of fruit and vegetables, that is the only system of its type worldwide.
Customer benefits
- Order pallets with fruits and vegetables are automatically assembled for deliveries to stores each day
- Approximately 75 SKUs are processed each day in the robot cells
- Approximately 50 SKUs are handled by staff in the manual picking area each day
- Integrated solution for the automated, priority-led pallet formation
- Optimum weight and volume utilisation through Dematic WCS specifications for pallet formation
- Order processing time of less than 30 minutes
- Compact system design provides additional free space for dispatch preparation and also gives options for further increases in incoming goods and throughput
- Design, supply of components, innovations, and IT from a single source
- Two year resident service contract
- Ergonomic design meets Danish safety regulations