Conveyor Systems Modernisations and Upgrades
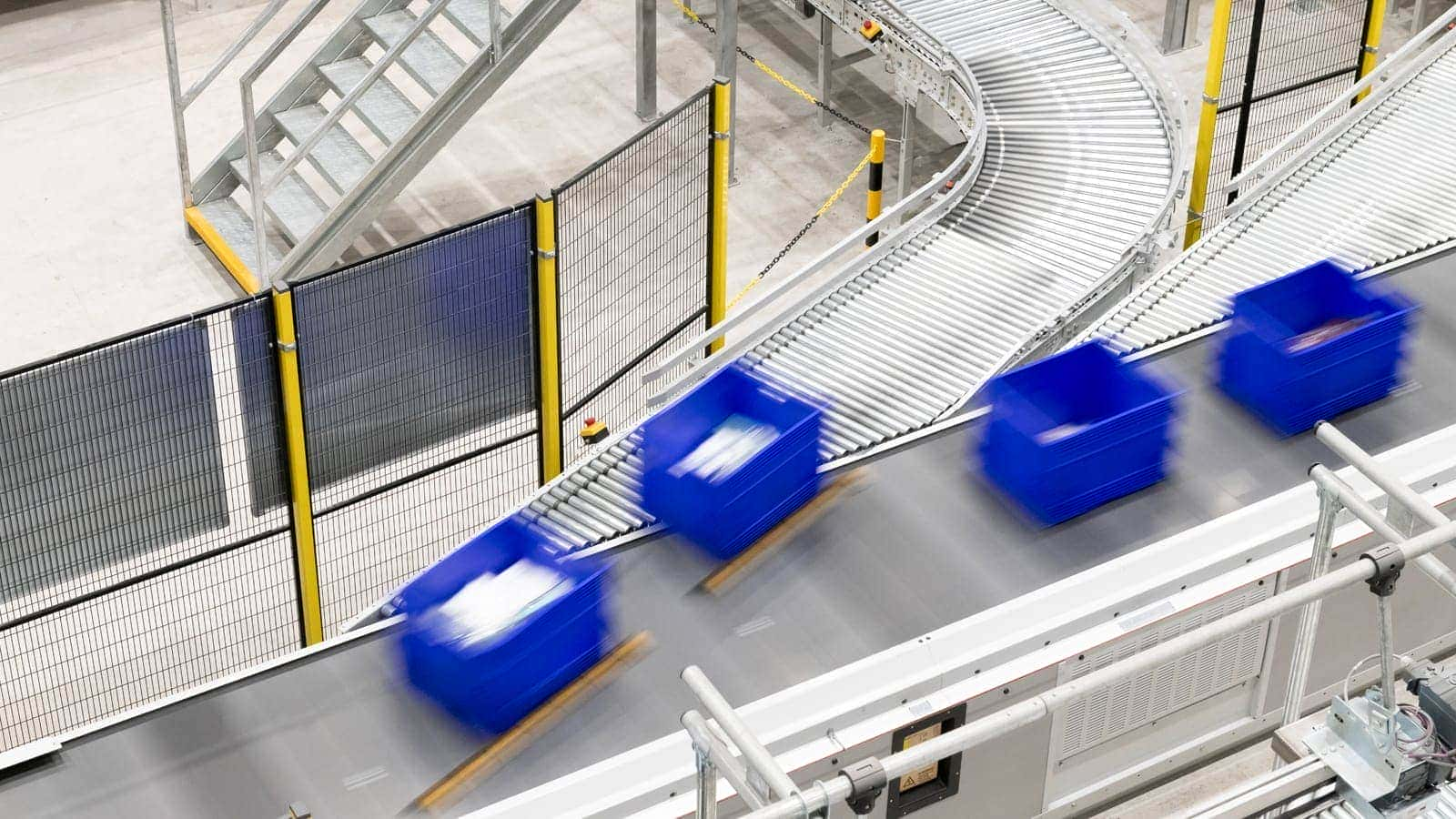
Dematic provides improved performance for existing conveyor system with modernisations and upgrades options. Your existing conveyor system may be experiencing these issues:
- Operational requirements have changed
- Conveyor requires re-configuration
- Existing conveyor is worn out and at end of life
- Existing conveyor cannot accommodate today’s demands
- Version of execution and controls software no longer supported
- Difficult to find replacement parts for older conveyor technology and controls hardware
Accumulation conveyor retrofits
The Dematic Non-Contact Accumulation Conveyor is ideal for existing operations that need to improve conveyor accumulation performance and reduce overall noise levels. It is designed to fit existing convey/sort system.
This next generation accumulation conveyor can replace poor performing conveyor and conveyor near or at their end of life. It is ideal for non-contact accumulation performance on declines.
New design features include:
- Non-contact accumulation for horizontal and decline applications
- All new configuration: sensor valve, linkage, brake, electronics, controls
- Coated rollers, drive belt and brake design reduce sound level
- Zero-pressure accumulation
- Fail-safe mode: brake is applied and drive belt released if no power/air
- Supports higher conveyor speeds for sorter induct
Dual zone controller
Upgrade your accumulation performance with the Dual Zone Controller 3. It is designed for retrofit to existing Dematic accumulation conveyor, model 9265. It replaces the previous version Dual Zone Controller 1 and Single Zone Controller.
The Dual Zone Controller provides effective carton/tote accumulation control. It can operate in multiple accumulation modes which are configurable. It controls one or two conveyor zones and uses electronic sensors to monitor load presence.
Dual Zone Controller 3 maximises conveyor accumulation performance. It’s simple to configure and change the accumulation mode. The clear cover and color-coded LEDs support at-a-glance status monitoring and diagnostics. The Switch Interface Module with status LED is mounted on the conveyor side channel for easy status viewing and access.
Additional Features and Benefits:
- Retrofit design enables easy plug & convey to existing conveyor
- Simple instructions and easy installation process
Quiet roller upgrade
Experiencing high noise levels in your operation? The Dematic Quiet Roller can be easily retrofitted into your existing conveyor systems. Built with a dual spring-loaded hex axle, the Dematic Quiet Roller is designed for universal application that fits easily into standard conveyor side channels. It improves workplace comfort and safety by damping roller noise.
Materials inside the roller shell and axle tips covered with urethane adaptors ensure a secure fit that reduces vibration and noise.
Additional Features and Benefits:
- Sealed precision bearings enable a quiet operation at all speeds
- Galvanised roller outer surface prevents corrosion and rust
- Coated roller (optional) provides additional sound damping and traction for decline conveyor
Carton aligner retrofit
The Dematic Carton Aligner is the ideal solution for operations that require improved carton singulation and alignment. The Carton Aligner resolves the following issues: side-by-side cartons, un-aligned carton flow, too much recirculation and carton jams. It is designed to output a single-file flow of cartons with alignment oriented to one side of the conveyor. This enables effective downstream barcode label scanning, carton alignment for label print/apply and accurate sorting/diverting.
The Dematic Carton Aligner fits existing conveyor and sortation systems. Installation is fast and cost effective, using the existing conveyor frame and drive systems.
Bulk flow container
The bulk flow conveyor upgrade includes new components that retrofit to existing Dematic bulk flow conveyor. The configuration includes the installation of silicon strips under the slider belt and a new return roller module. Operating sound level and energy use is minimised by reduction of friction on the metal slider bed and return roller surface.