Maximize Warehouse Storage Space
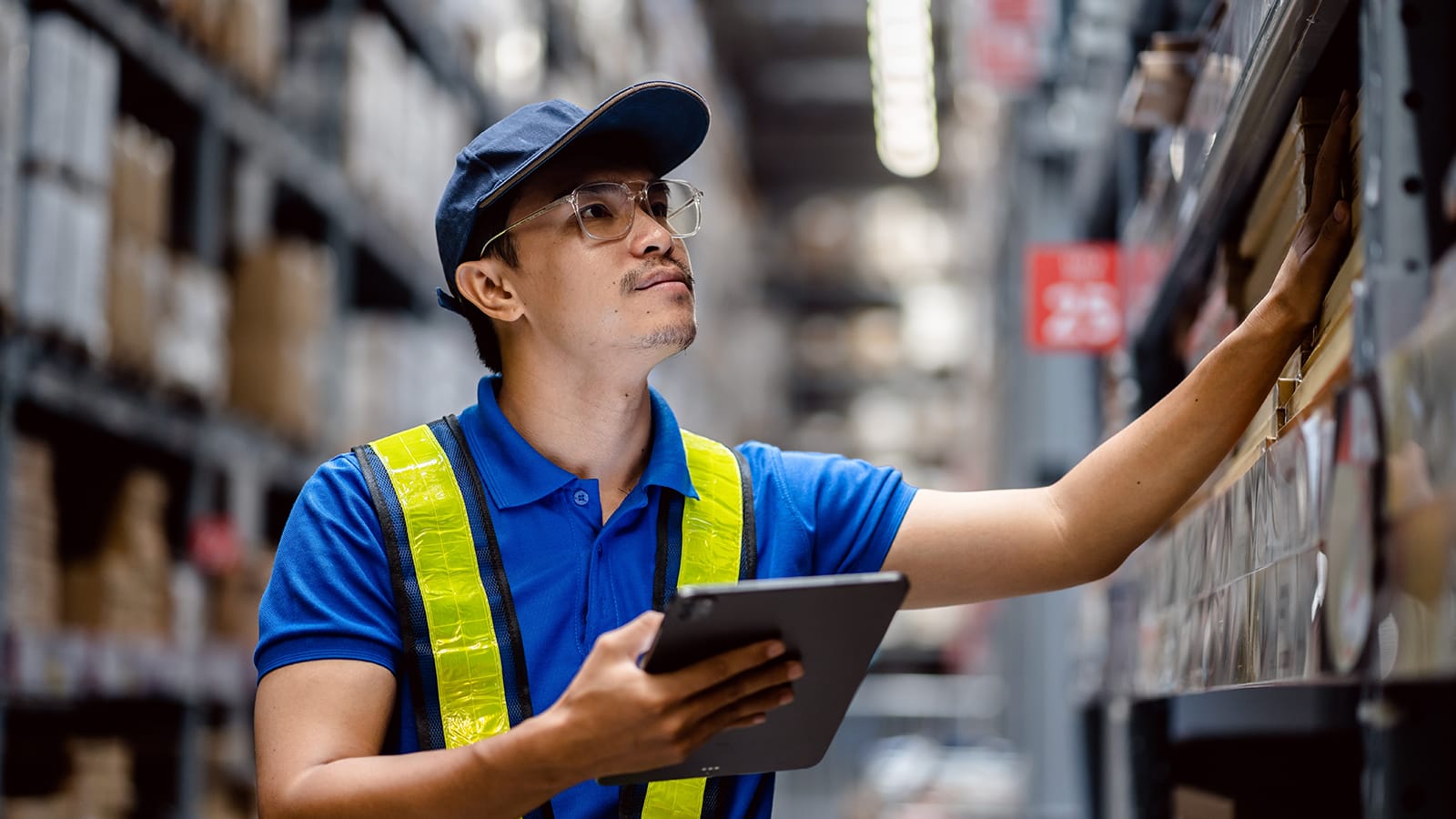
Improving storage density without compromising usability
Ask any warehouse manager to list their biggest challenges and lack of space will most likely be one of the top issues. Many organizations resort to outside storage options or costly expansions to remedy this challenge. However, it’s always worth looking at the storage density in a facility — sometimes existing space can be more efficiently used, avoiding the need to expand your facility or move inventory offsite.
Storage density vs. utilization
There are many solutions to provide dense storage. But, depending on your inventory mix, some of these alternatives may have significant and costly side effects.
The simplest means of using available warehouse space is to pack it from floor to ceiling with inventory — for example, installing high-bay pallet racking for palletized goods, building mezzanine floors to add shelving for cases, or simply moving items to unused overhead space. While these storage strategies may technically provide the densest use of space, they don’t allow product selectivity or easy access. Also, making these strategies work requires costly labor to shuffle and dig through storage to access the inventory.
To simplify this, some businesses allocate each storage bay or shelf to specific SKUs, but this in turn reduces storage density when space is left as available as inventory is reduced. Finding the best solution requires finding the right balance between density and accessibility.
Automation for high-density and good selectivity
Automation can improve selectivity in high-density storage. Machines and robotics reduce the physical space required for access to retrieve and store stock with, for example, much narrower aisles. Automation provides many additional benefits, such as better inventory management, 24/7 operation, predictable logistics, and reduced labor costs.
Whether you need to store pallets, cartons, or individual small items, an automated system can help you get the most out of its space.
Benefits of automated high-density storage
Maximized and optimized use of space
Reduced need for expansion or external storage
Better inventory management and data visibility
Reduced labor requirements
Improved retrieval speed and accuracy
Reduced product damage and shrinkage
Ideal for temperature-controlled storage environments
High-density automated storage for pallets
There are several manual and semi-automated solutions available for pallet storage that improve storage density over traditional pallet racking. Storing multiple pallets in double-deep selective racking, pallet live storage, drive-in racking, push-back racking, or using satellite storage all provide better use of space, but all come inventory accessibility challenges and increased operational costs. These two automation solutions can be better options:
Automated Guided Vehicles (AGVs) are robotic vehicles programmed to handle palletized goods throughout a facility. This includes truck unloading and loading, block stacking, and putting away and retrieving pallets from storage racking.
Narrow-Aisle AGVs are designed with storage density in mind, operating in tight spaces with small turning circles, which allows racking layouts to be condensed. The selectivity of standard racking is maintained, and more pallets can be stored overall.
Dematic AGV systems follow configurable guide paths to optimize storage, picking & transport functions in a wide variety of environments.
Automated Storage and Retrieval Systems (AS/RS) further increase density with tight access aisles for cranes that transfer pallets of inventory in and out of the racking. AS/RSs can be very tall to make use of facility height. Pallets are stored single, double, or — with the use of additional satellite carts — multiple deep.
Dematic offers warehouse storage systems & solutions that organize & control inventory on pallets, cartons & garments-on-hangars.
High-density automated storage for cases and totes
Automated storage for cases or items in totes can reduce the required footprint of storage to as little as one quarter of that needed for traditional shelving, removing access aisles for people and pick carts, and organizing the stock to reduce wasted space in pick locations. Automation options include:
Multishuttle systems are powerful AS/RSs specifically for handling cartons, totes, and trays. Products are stored in shelving accessed by shuttles — one per level of storage — which drive up and down the aisles, reaching into the shelving to retrieve or store stock.
With very little physical space needed between cases, levels, and aisles, the storage density of multishuttle systems is excellent. Additional benefits include high-speed, sequenced retrievals, low power requirements, and high accuracy.
AutoStore is an extremely high-density storage and buffer system that specializes in handling small items. AutoStore optimizes storage density, allowing four times more inventory than conventional storage systems in the same space.
Items are stored in bins that are efficiently stacked in a storage grid. Robots that travel across the top of the storage grid access the bins to store and retrieve them. With no aisles required for machinery, more space can be dedicated to storage. And, because of its flexible design, AutoStore storage systems can be built to fit almost any available space — around building columns, over walkways or other warehouse areas, and in odd-shaped spaces.
AutoStore is an ultra high-density storage and buffering system for goods-to-person piece picking that increases the efficiency.