Dematic Wins Technology Excellence Award for Robotics-Logistics
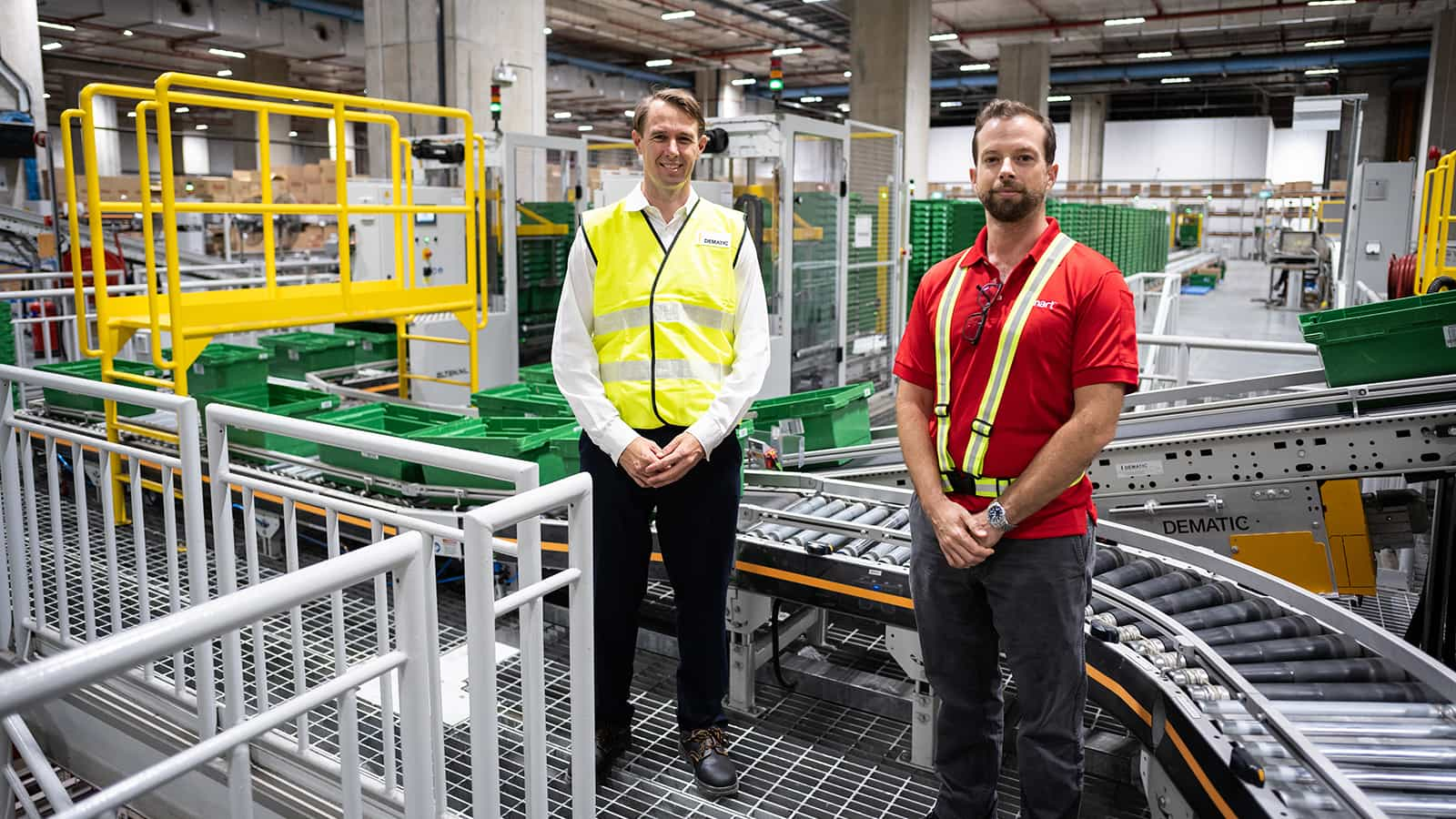
May 20, 2022
SYDNEY – As the global pandemic hit and forced lockdowns, the public relied heavily on online means to go about their daily lives – turning to their personal gadgets to complete their banking needs, attend meetings, and shop for groceries. But with the new normal came its challenges, with online services such as RedMart realising that the old method of manually hand-picking orders to pack and send to customers would no longer cut it and keep up with the increasing demand.
Thanks to the innovative solution from Dematic, the RedMart West Fulfilment Centre was able to increase its logistical prowess through automation. The keys to the solution were the Dematic Goods-to-Person (GTP) Picking system and the Dematic Multishuttle® system. With the Multishuttle system, products are automatically stored in high-density racks by robotic shuttles and totes are automatically transported between storage locations and pick stations, eliminating the need for operators to travel around the facility. Products are delivered to operator pick stations automatically, increasing picking speeds and productivity and reducing picking errors.
Thanks to this solution that has increased productivity, safety, and resilience to disruptions exacerbated by the global pandemic, Dematic collected the Robotics-Logistics award at the recently concluded Technology Excellence Awards, presented by Singapore Business Review. In its fourth year, the awards event lauds companies in Singapore that have pioneered ground-breaking IT products, solutions, or initiatives that are leading the technological revolution and digital journeys of their respective industries.
The decision to install a high level of automation at the facility was made well before the onset of the pandemic, but the importance of the automated solution in RedMart’s business has been underscored by the pandemic.
With the GTP Picking system at RedMart, operators can now pick and pack 500 items in the same time that they used to take to pick 100 items manually. In its previous setup, RedMart operators would have had to manually travel around aisles of shelving to pick the items required for orders, and the subsequent loading and unloading of trolleys resulted in a highly inefficient process that was not only time-consuming but also prone to errors that are difficult to detect.
The Dematic solution also includes order fulfilment of fresh produce in multiple temperature zones, including a freezer area. Orders are transported through the various picking areas of the facility by an intelligent routing conveying system and are consolidated at ergonomic packing stations. They are then conveyed and automatically sorted to specific delivery vehicles by a high-rate sorter.
“By limiting touchpoints, the solution improves speed, productivity, and hygiene,” Dematic said, adding that the solution has increased throughput, with a higher capacity in a compact footprint.
Another key factor in developing the overall infrastructure for the RedMart West Fulfilment Centre was the building footprint. In Singapore, a big component for businesses is the cost of space. When RedMart first started talking to Dematic, they were receiving less than 2,000 orders per day and had around 5,000 products in their range. And so, the RedMart West Fulfilment Centre needed to be designed to handle a significantly greater number of orders and products daily to keep up with the rate at which consumers turned to online platforms to purchase their groceries.
“RedMart realised they would not be able to find the space or the workforce to meet their growth target using their current practices,” Dematic said.
Once the solution was in place, RedMart’s sales jumped by more than four times during the start of the pandemic, with unique visitors to the website rising by more than 11 times. Having the Dematic solutions implemented on time, RedMart was able to fulfil these demands without the shock of additional costs or supplementary solutions.
About Dematic
Dematic is a global leader in supply chain automation solutions featuring advanced technologies and software empowering the future of commerce for its customers in manufacturing, warehousing, and distribution. With research and development engineering centers, manufacturing facilities, and service centers located in more than 26 countries, the Dematic global network of approximately 10,000 employees has integrated and supported automation solutions for many of the world’s leading brands. Headquartered in Atlanta, Dematic is a member of KION Group, one of the world’s leading suppliers of industrial trucks and supply chain solutions.
Disclaimer
This release and the information contained herein are for information purposes only and do not constitute a prospectus or an offer to sell or a solicitation of an offer to buy any securities in the United States or in any other jurisdiction. This release contains forward-looking statements that are subject to various risks and uncertainties. Future results could differ materially from those described in these forward-looking statements due to certain factors, for example, changes in business, economic, and competitive conditions, regulatory reforms, results of technical studies, foreign exchange rate fluctuations, uncertainties in litigation or investigative proceedings, and the availability of financing. We do not undertake any responsibility to update the forward-looking statements in this release.