Sigma Healthcare Supports Growth by Automating Operations at New Perth and Brisbane DCs with Dematic
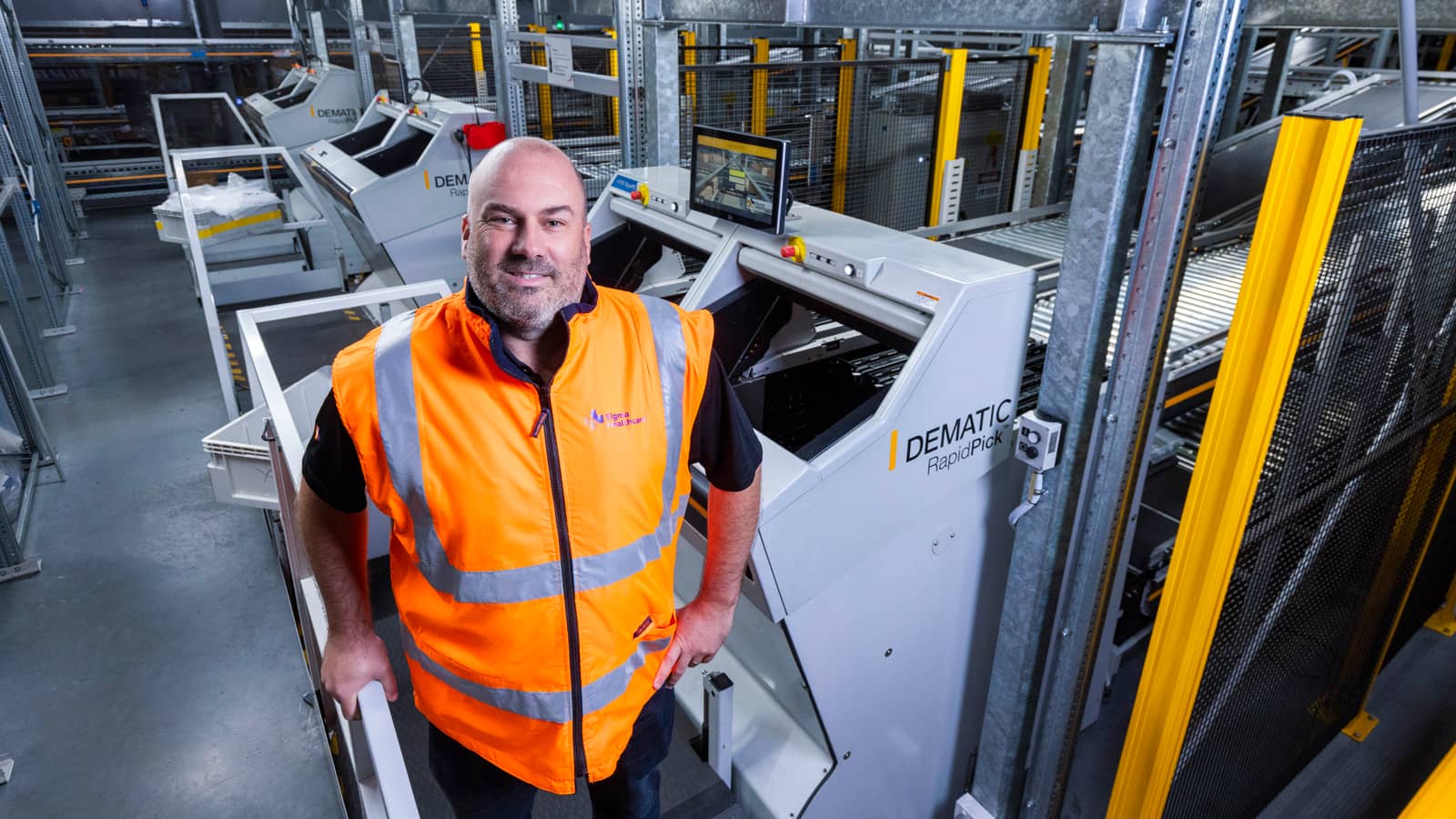
Sigma Healthcare - Perth and Brisbane, Australia
- Sigma Healthcare is a leading Australian full line wholesale and distribution business catering to community and hospital pharmacies. Employing over 1,100 team members, Sigma services over 4,000 pharmacies and operates 10 distribution centres (DCs) nationwide.
- Sigma has one of the largest pharmacy networks in Australia, with over 1,200 branded and independent pharmacies, including some of Australia’s best known pharmacy retail brands such as Amcal, Guardian, Pharmasave, Chemist King, WholeLife, and Discount Drug Stores, which collectively account for close to 20% of consumer spend in pharmacy in Australia.
Paul Brown, National Operations Manager, Logistics at Sigma.“The competitiveness of the pharmaceuticals industry today is very high compared with previous years. Pharmacies are constantly pushing Sigma as their sole distributor for increased service levels, which were just not achievable at previous operation rates. By initiating a more innovative approach to picking operations, we can make the most of our two new DCs with advanced automation technologies ensuring the highest efficiency.”
Sigma’s Shift To Self Sufficient, Automated Distribution Centres
As part of its network optimisation strategy to increase its competitiveness in the pharmaceutical industry, Sigma implemented materials handling solutions from Dematic – an intralogistics innovator that designs, builds, and supports intelligent, automated solutions and software for retail, manufacturing, and distribution operations.
Sigma selected the Dematic Goods-to-Person (GTP) Picking Solution as the central system to improve operational efficiencies at its two new DCs in Perth and Brisbane. Sigma’s decision stemmed from previous challenges experienced from legacy systems deployed at other DCs, which was curtailing the ability to continue to improve service delivery to customers.
The central objective Sigma had for the new system was for an automated solution that was modular and capable of expansion. The key operational improvements were enhanced productivity and accuracy rates achieved through the reduction of manual put away, replenishment, and picking processes with an end goal of the DCs processing the majority of their volume through automated picking procedures.
“By automating operations with the Dematic solution, we wanted these new DCs to be robust and innovative, all whilst meeting Australian Standards and Sigma’s own quality parameters. Likewise, we wanted to offer service differentiation through improved DIFOT (delivery in full, on time) and an advanced ability to manage order volume growth,” added Paul.
A solution to automate and streamline operations
Sigma selected Dematic as its automation partner due to its track record of successfully implementing automated solutions to manufacturing and distribution operations in Australia, as well as its global expertise in supply chain optimisation and warehouse innovation.
The overarching goal was to modernise its new DCs with the latest in automated picking technology. The Dematic GTP Picking Solution was a step up from the previous technology deployed at other DCs, as it provided a solution to better meet the desired productivity rates, whilst still supporting the traditional voice picking systems in place.
The solution concept focuses on improved picking productivity with a GTP and A-Frame solution moving more volume through the system.
Dematic Software controls operations by optimising order fulfilment, from direct picking into right-sized shipping containers to reducing cycle times, labour costs, and shipping/transportation costs. Dematic Software interfaces with Sigma’s existing Warehouse Management System (WMS).
Paul Brown, National Operations Manager, Logistics at Sigma.“The increased demand for products and services Sigma was experiencing drove us to implement a DC picking strategy capable of delivering efficiency and productivity rates that matched the high demand,”
“The Dematic GTP Picking Solution delivers items directly to workstations – eliminating the need for operators to manually locate and retrieve items by travelling across the DC floor. The solution enhances operator performance by combining high-density, secure storage with the rapid rates and accuracy of directed picking from the ergonomically designed workstations,” said Darren Rawlinson, Dematic’s Regional Solutions Development Director, APAC.
The GTP solution receives inventory at decant workstations where operators scan barcodes and transfer items into inventory totes, which are automatically weighed and then conveyed and stored in three aisles of Dematic Multishuttle storage system. This ensures maximum inventory accuracy.
For order picking, inventory totes are retrieved from the Multishuttle system and sent to the Dematic Rapid Pick workstations, where lights and graphical instructions direct operators to pick the required items from the inventory tote. The inventory totes are then returned to storage, ready for the next order. Completed orders are transported to a Multishuttle storage buffer ahead of despatch. When the delivery run is ready, the totes are retrieved from the buffer prior to automated lidding, labelling, weighing, and scanning, and routed to the despatch sorter.
Additionally, the system can operate in a temperature controlled environment, which is required for select pharmaceutical products that must be stored between 2° and 8°C
The Solution Rollout
Throughout the rollout phase of the projects, Dematic supported Sigma with in-house teams in Perth and Brisbane. Dematic’s expertise in software, controls, and project management ensured that the deployment achieved the best performance. The Brisbane DC was the first to go live, with the Perth DC reaching completion six months later.
“We worked alongside Sigma’s in-house project management teams throughout every stage of implementation, including the rollout and go live. This collaboration ensured that the Sigma team understood how the system was going to work and were on-board with the fundamentals of it being integrated within the new DCs,” said Glenn Barnes, Industry Manager Grocery & General Merchandise at Dematic.
Go-Live Training
“During the rollout, we had a ‘ramp up’ period where we supported Sigma through important milestones. Additionally, our residential technology support team worked alongside the project management team to answer any queries and ensure technical issues were dealt with immediately,” added Glenn.
Throughout the rollout, Dematic encouraged a “train the trainer” approach to developing a good working knowledge and understanding of the system amongst key operational and management personnel at Sigma, who then trained all Sigma employees working with the system.
“Dematic worked in collaboration with our in-house project management teams at both DC sites, which really helped to ensure that our own staff understood the changes the new system was going to have on operations and how it was going to work,” said Paul. “Dematic’s support and expertise throughout the rollout and the entire project made for an easy transition, and with their constant assistance, we were confident that the new system would perform at its best.”
Service and Support
An ongoing Dematic service and support program optimises system uptime and continuity of production efficiency. It includes 24/7 support for all equipment, controls, and software with a residential service team located on site.
“By proactively working to reduce system downtime, we can reduce the overhead costs of system maintenance for Sigma. The program offers assurance to Sigma from us (the system designers) that their system is operating at peak efficiency,” said Darren.
Benefits of the New Solution
Integrating an advanced automated picking system for improved operational efficiency has been a big benefit for Sigma overall.
“The GTP solution is a standout innovation for streamlining DC operations – Sigma is now equipped to match the high level of demand and competitiveness they are currently experiencing,” said Glenn.
“The system optimises the entire picking and delivery process by organising orders accurately and efficiently, and much faster than manual operation,” added Glenn.
For Sigma, warehouse and logistics has been an area of significant focus over the past three years. Through the deployment of the Dematic and other solutions to its network of new DCs, Sigma has subsequently made significant progress to its initiated business transformation program (Project Pivot), which aims to deliver $100+ million in efficiency gains by the end of the 2021 financial year.
Additionally, the Dematic GTP Picking Solution provides a safer workspace for all DC staff, meeting all current regulations that apply to Sigma’s DCs in Brisbane and Perth, such as Work Health and Safety, OH&S, Guide to Good Distribution Practice (GDP) for Medicinal Products, and the current health government regulations around COVID-19.
Sigma has been able to fulfil current and future order volumes with an increased number of stock keep units (SKU) to accommodate volume growth in line with Sigma’s business plans through to 2027.
“The modular and scalable solution provides us with the flexibility to optimise current operations and to expand as our business grows. Likewise, the ability to manage logistics costs and forecast budgets has been a significant benefit to us” said Paul.