Geographic & Channel Expansion with Automation
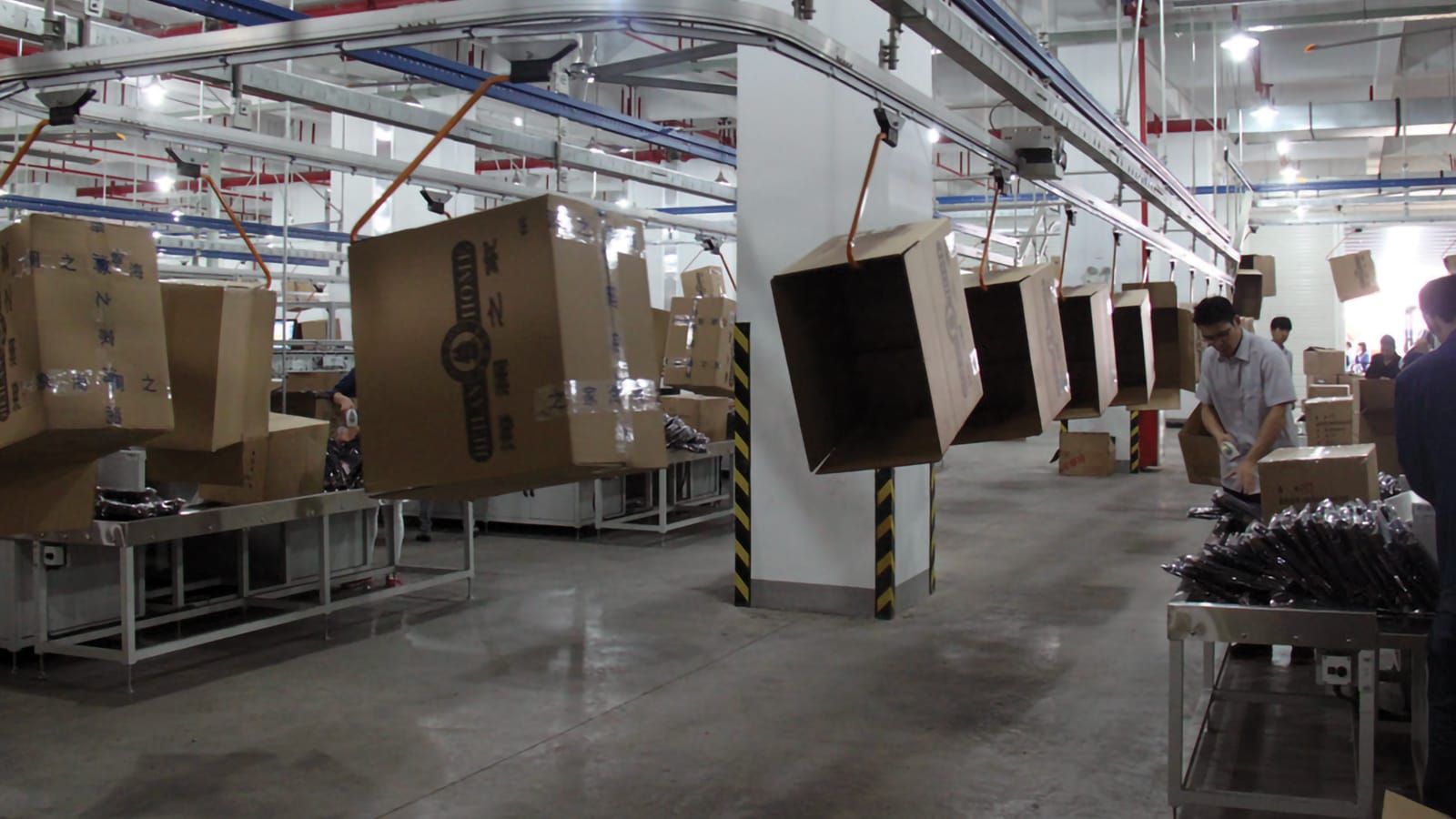
Significant investment in automated logistics with Dematic has helped leading Chinese clothing distributor Heilan Home expand rapidly in recent years, its turnover increasing by 50% to 12.7 billion RMB in 2013.
During its logistics transformation project, Heilan Home has been continually building its supply chain to manage rapid growth with an Intelligent Warehouse System (IWS) that features high levels automation.
The challenge
Heilan Home is located in Xinqiao, Jiangyin, Jiangsu Province in China.
As a major clothing company, it focuses on managing brands, producing and distributing high-end woolens, suits and business clothes under four key brands – Heilan Home, Eichitoo, Bettsale and Sancanal – creating its distinctive brand “Heilan Home - Men’s Closet”.
Driving business transformation
Operating under a brand and platform model, Heilan Home retains responsibility for product development, brand management, supply chain activities and sales network management, while outsourcing clothing manufacture and shipping.
Heilan Home operates a growing network of chain stores. This enables the business to unify and manage store presentation, supply chain and service standards, with franchisees sharing sales income with Heilan Home.
Importance of logistics
Heilan Home Chairman, Zhou Jianping, places a high priority on supply chain efficiency.
In Huashi, Jiangyin, Heilan Home’s Logistics Park is located opposite its R&D facilities and comprises 24 warehouses, picking and sortation centers and delivery halls.
The buildings cover 8,500,000 square feet (790,00 square meters) and represent an investment of 1.6 billion RMB, including Dematic’s Intelligent Warehouse System (IWS), which went live in November 2013.
The IWS comprises two ASRS, three delivery halls, and one distribution center. Heilan Home’s Logistics Park has a design inventory of 14,640,000 cartons and the storage capacity is 80 million products.
Infeed and outfeed capacity can both reach up to 320,000 pieces per day. Zhang Judi, Director of Heilan Home Storage & Delivery Center, said the IWS is the largest and most advanced automated logistics system in the Chinese apparel industry.
Initially, Heilan Home’s Logistics Center consisted of single storey warehouses, which were run manually. As the business grew, the single storey warehouses were modified into two-storey facilities, while newly-built warehouses were designed with three or four levels.
Integrated logistics systems
Two ASRS are located in Buildings 9 and 10, a picking zone in Building 16, hanging garment systems in Building 17, returns processing in Buildings 18, 19 and 20 and delivery halls in Buildings 21, 22 and 23.
Dematic’s 89 foot high ASRS contains 73,200 pallet locations serviced by 30 SRMs, 274 pallet conveyors, 8 shuttle cars and high-rate sorting systems.
The IWS covers automated storage, batch picking, automated sorting, delivery and returns processing and comprises ASRS, voice picking, case conveyors, spiral conveyor systems, crossbelt and pop-up wheel sortation systems.
With each item identified by a unique barcode, the company can accurately manage storage, distribution and sales. The IWS also supports Helian Home’s growing online business activities, with automated check weighing in its eCommerce warehouse eliminating costly delivery errors, enabling the business to achieve online order delivery accuracy of close to 100%.
Logistics operations
Being the only DC for Heilan Home, the Logistics Park never really has peaks or low seasons. Because Heilan Home is responsible for suppliers’ inventory management, products constantly flow into warehouses.
At the same time, Heilan Home needs to replenish goods to stores in a timely manner to maintain required stock levels, which means processes like infeed and outfeed basically never stop.
Garments in Heilan Home are largely picked from cartons, which accounts for about 70% of sales, with the remainder picked as hanging garments.
Infeed storage
After delivered goods have passed QA checks on receipt, they are inducted into the ASRS in Buildings 9 and 10.
Staff take goods out of cartons, scan the product barcodes one by one, and put the stock into Heilan Home standard cartons. To optimize space, overhead conveyors are used in the Receiving Zone for carton replenishment and recycling.
Three scanning and repacking lines contain 36 workstations and can handle up to 160,000 products per day. Operators then palletize cartons, scanning the carton code and pallet barcode. Pallets are then transported to the conveyor lines in front of the ASRS by forklift for put-away.
Picking and outfeed
Packaged garments pallets from Warehouse 9 and 10 are retrieved by SRMs and fed out onto the fourth floor. When pallets arrive at conveyor lines in front of the ASRS, operators retrieve cartons from the pallets and put them onto case conveyors, which transports them to a picking zone.
After fast-moving SKUs are outfed, they are transferred by inclined case conveyors to the third floor of Warehouse 9 and 10, where items are picked using voicedirected picking.
Medium-slow moving goods are outfed on the fourth floor for replenishment of floors 4-6 of Warehouse 16.
Two crossbelt sorter lines across three levels can process orders for up to 500 stores simultaneously, handling up to 40,000 items per hour.
Sorted orders are sealed, labelled and wrapped. Orders and goods from the repacking zone are merged onto case conveyors and transferred to three delivery halls covering an area of 375,000 square-feet (35,000 square-meters).
Products are then sorted by pop-up wheel sorters to the appropriate dispatch lanes and loaded onto trucks for shipping.
Two shipping waves occur every day – one in the morning, and one in the afternoon. Heilan Home achieves an on-time delivery rate of over 98%, with stores in Yangtze River Delta receiving goods same day, and deliveries to its most remote stores in towns like Wulumuqi taking up to five days.
Hanging garments
Hanging garments are stored and picked in two seven-floor automated hanging garment warehouses, with each level linked by conveyors.
The warehouses use an overhead rail conveyor system with a total capacity of 1.2 million products.
Taking Warehouse 23 as an example, the first floor is the delivery hall, the second floor is a sortation zone, and the third to seventh floors are utilized for receiving and storage.
A total of 183 rail tracks were installed in the hanging garment warehouses, enabling batch picking for up to 183 stores.
Before outfeed, hanging garments are taken off hangers and put into cartons, which are merged with flat-packed goods in the delivery hall. They are then consolidated for shipping.
The automated hanging garment warehouses are also equipped with empty-carton conveyors and automated wrapping machines.
All outwards products flow into delivery halls where they are loaded onto trucks for shipping to different regions.
This means that goods from different warehouses have to arrive at the same time in the delivery hall.
Processing returns
Unlike other clothing companies which typically wholesale their goods, Heilan Home owns the operating and managing rights of its stores.
When product sales cycles end, last season’s SKUs are returned to the Logistics Park where they are processed into sizes and styles, enabling the stock to be consolidated for sale. Because of this, Heilan Home handles a lot more returns processing than many other clothing companies.
All incoming returns are scanned at Warehouse 18 to update inventory levels and are then put into totes. When the stock enters Warehouse 19, a QA inspection checks for any damage that may make the goods unsuitable for sale.
After product pre-sortation, where clothes are sorted into different types like trousers, shirts and T-shirts, the stock is buffered before being automatically sorted into batches in Warehouse 20.
Conclusion
Dematic’s IWS has supported the rapid growth of Heilan Home, and delivered multiple benefits:
- A range of integrated logistics systems which deliver Goods-to-Person, have significantly increased operating speed and accuracy with order fulfillment taking eight hours instead of 24.
- With seven times the capacity of a conventional warehouse, the introduction of ASRS has optimized space efficiency and reduced land costs.
- Batch picking has enabled the business to significantly decrease manual picking, reducing labor costs by more than 60%. The good working environment also attracts higher quality workers, with students and college graduates making up a large percentage of staff.