Logistics Provider VEYER Looks to Dematic for the Technology to Deliver the Perfect Order
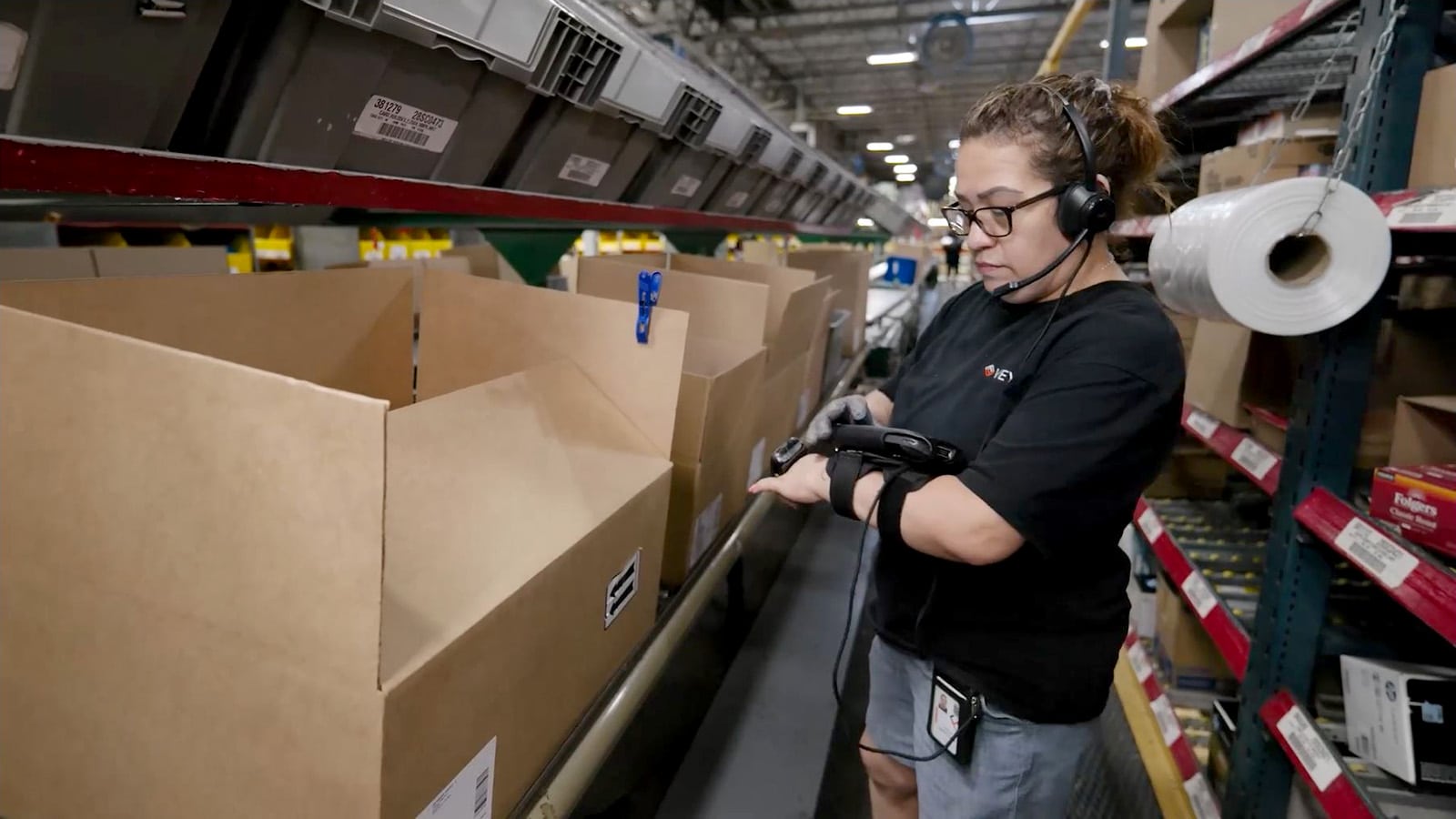
Dematic pick-to-voice system provides fast, efficient order fulfillment
VEYER is a third-party logistics (3PL) company based in Boca Raton, Florida with a network of facilities throughout the United States and Canada. VEYER prides itself on radical transparency with no excuses in delivering the perfect order every time. As a result, they are continually looking to improve their technology to ensure that every order is accurate and meets customer expectations.
The challenge
As a 3PL, VEYER is in the business of delivering for their customers on a daily basis. Relying on dated, labor-intensive processes is simply not an option, so automation is not an option — it’s a necessity.
VEYER looked to Dematic for the technology and partnership to provide the best possible supply chain results for its customers.
The solution
The process begins when the Dematic Software system receiving an order from the VEYER host platform. A carton erector builds a carton that is sized for the order and the system generates a packing slip with a unique barcode, which goes in the carton. The carton runs through a scanner, and a shipping label is generated and applied to the carton.
The barcode contains the SKU data, the product description, the quantity of the SKU to be picked, and where it's located within the building. The Dematic Software routes the carton to the zones that have picks for the order.
Operators scan the carton, and their pick-to-voice devices tells them what SKU to pick and how many. If the order is not complete, the system knows the order has picks in other zones and routes the carton to the next available zone.
When the order is complete, it is routed to a QA packing department. A weigh check verifies the order, making sure the carton weight is equal to the weight expected for the order.
The system adds dunnage to the completed carton, and it’s taped up and sent on to the shipping dock. The VEYER sortation system routes the carton to the appropriate door for it to be delivered the next day. Monitors show the entire system so operators and managers can see the carton being routed efficiently throughout the system.
The result
VEYER now has the capacity and throughput it needs to be competitive now, with the ability to expand in the future. VEYER is leveraging automation and technology to be fast, efficient, and accurate to deliver the perfect order every time.
John Gerringer, Director, Maintenance Engineering at VEYER Logistics“VEYER is leveraging automation and technology to be fast, efficient, and accurate.”