El nuevo centro de distribución de Asahi logra un aumento de la productividad del 250% con un sistema automatizado
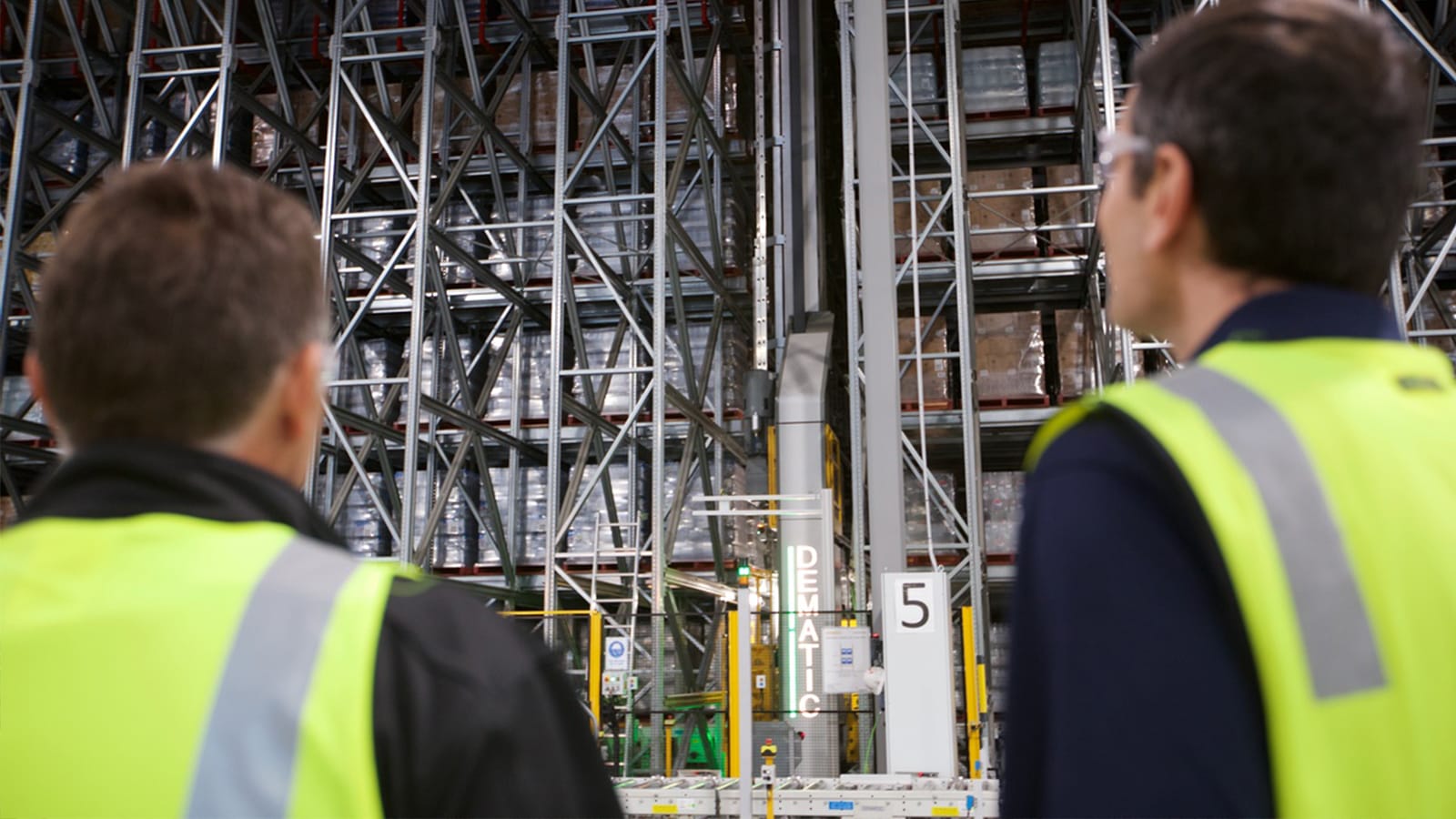
Asahi Beverages es una empresa líder de bebidas que produce y distribuye productos alcohólicos y no alcohólicos en Australia y Nueva Zelanda. Con una historia rica y variada, Asahi comercializa bebidas de calidad, y cuenta con una sólida cartera de marcas familiares consolidadas y productos innovadores recién llegados al mercado.
Asahi Beverages es miembro de Asahi Group Holdings, una de las principales empresas de bebidas de Japón, e incluye algunos de los negocios de bebidas con más éxito de Australia y Nueva Zelanda, como Asahi Lifestyle Beverages (antes conocida como Schweppes Australia), Asahi Premium Beverages, Independent Liquor y The Better Drinks Co.
En la actualidad, Asahi Beverages emplea a más de 2.100 personas en Australia y Nueva Zelanda.
Dejando atrás el sistema manual
Asahi tiene varios centros de distribución en Australia. Anteriormente, en Brisbane, Asahi operaba en varias ubicaciones y utilizaba carretillas elevadoras manuales para apilar bloques, lo que suponía muchas desventajas y desafíos.
Recientemente, Asahi unificó sus múltiples centros de Brisbane en un solo centro de distribución. Con el desarrollo del centro de distribución de Heathwood, Asahi decidió cambiar a una solución de almacén automatizado, ya que anteriormente tenía un sistema que requería mucha mano de obra.
"Cada camión que entraba tenía que ser descargado por una carretilla elevadora, después teníamos que recibir el papeleo manualmente, comprobar los palés manualmente, mover los palés a la ubicación de almacenamiento y luego hacer todo eso a la inversa para recogerlos", dijo Nathan Lucinsky, Director de Heathwood DC, Asahi.
Al tomar la decisión de consolidar sus centros en un solo centro de distribución y actualizarlos a una solución automatizada, Asahi quería conseguir una serie de ventajas, como reducir costes, mejorar la eficiencia y la productividad y poder satisfacer mejor las necesidades de sus clientes.
Sistema automatizado de almacenamiento y recuperación
Un factor clave en el proceso de toma de decisiones de Asahi a la hora de buscar una solución de almacén automático que satisficiera las necesidades de su centro de distribución de Heathwood fue trabajar con una empresa que comprendiera el mercado local. Asahi eligió a Dematic, ya que ha demostrado su capacidad para realizar proyectos similares en Australia.
"Como la nueva solución de automatización sería la primera vez que se implementaba, para Asahi era fundamental hacerlo bien", dijo Dominic Figliano, Director de Proyectos de Dematic. "Durante la fase inicial de diseño y desarrollo del concepto, Dematic consideró una serie de alternativas de almacenaje de bahía baja y bahía alta, pero después de evaluar los requisitos de almacenaje de Asahi, supimos que la mejor solución para ellos era el Sistema Automatizado de Almacenaje y Recuperación (ASRS) de seis satélites de profundidad."
Las estanterías de gran altura en Asahi Heathwood DC tienen 13 niveles de altura y 34 bahías de profundidad, y el ASRS se extiende a seis posiciones de palés de profundidad a cada lado de las seis grúas, a las que se accede mediante carros satélite. En total hay aproximadamente 31.500 posiciones de almacenamiento de palés.
"El ASRS que construimos para Asahi utiliza la grúa más nueva y rápida de Dematic, la 1200-1. También es el sistema de satélites más alto que hemos construido en Australia", dijo Dominic.
El viaje de un palé comienza en uno de los dos centros de producción de Asahi en Queensland. A continuación, el producto se transporta al centro de distribución de Heathwood en camión. Cuando el camión llega al lugar, el conductor retrocede hasta el muelle de patines y, a continuación, acciona el dispositivo automatizado para alinear el remolque y comenzar el proceso de descarga. Los patines se extienden hasta la parte trasera del remolque, las bolsas de aire se disparan y levantan los palés del suelo del remolque.
En este punto, los patines se repliegan de nuevo en el muelle, las bolsas de aire se desinflan y los transportadores de cadena llevan los palés a nuestro circuito principal de transportadores en el almacén.
A continuación, los palés se someten a una comprobación automática de perfil en la que se validan con respecto a los requisitos de especificación del sistema ASRS. El bucle de transportadores lleva el palé a la estación de descarga, donde el sistema ASRS toma el relevo.
La grúa eleva y conduce el palé hasta la ubicación de almacenamiento asignada y, a continuación, un carro Supercap toma el relevo y conduce ese palé hasta el satélite y lo almacena.
El ASRS está dirigido por el software Dematic WCS. En la sala de control automático y también en las estaciones de trabajo de la planta, los operarios interactúan con el sistema WCS GUI y también disponen de un sistema SCADA que pueden utilizar para supervisar el estado del sistema en tiempo real.
Además del ASRS, Dematic también integró equipos de terceros, incluidos los muelles de patines, una enfardadora, aplicadores automáticos de etiquetas y un inversor de palés.
Implantación del sistema
Antes de la construcción del centro de distribución de Heathwood, Dematic participó en el proceso de elección de un nuevo emplazamiento para el nuevo centro de distribución con el fin de garantizar que la ubicación se ajustara a los requisitos de almacén de Asahi, así como a los requisitos del nuevo sistema que Dematic había diseñado.
"El centro de distribución de Asahi era un terreno virgen cuando empezamos a trabajar en la instalación del ASRS, lo que supuso una serie de retos", dijo Dominic. "Como el centro de distribución era todavía una obra en construcción, había constructores, electricistas, hormigoneros y otros contratistas y trabajadores con los que teníamos que coordinarnos y trabajar conjuntamente. Por ejemplo, tuvimos que coordinarnos estrechamente con la instalación de rociadores contra incendios para asegurarnos de que los rociadores encajaban en las estanterías y cumplían los requisitos."
La estrecha coordinación y la programación también fueron cruciales para coordinar los diversos equipos utilizados por todos los trabajadores, de modo que los plazos del proyecto se mantuvieran dentro de lo previsto. Dematic tenía dos equipos en la obra, que utilizaban hasta dos grúas de 80 toneladas, cuatro plataformas elevadoras y dos elevadores de tijera.
"Tuvimos hasta 50 personas in situ y completamos parte de la instalación durante la noche para asegurarnos de mantener el calendario y entregar el proyecto a tiempo".
Otro aspecto clave del despliegue del sistema fue la formación que Dematic impartió al equipo de Asahi una vez finalizada la instalación.
"Proporcionamos formación de superusuario a Asahi, lo que supuso formar pequeños grupos y ofrecerles formación teórica y práctica sobre el uso del nuevo sistema. Estos superusuarios pudieron formar a otros trabajadores de Asahi DC en el futuro", explica Dominic.
Como el centro de distribución de Heathwood tiene estanterías altas, se prestó especial atención a la seguridad en el trabajo en altura.
El despliegue del nuevo sistema se completó con éxito en mayo de 2019.
Beneficios del nuevo sistema
Las ventajas más destacadas del sistema Dematic son la alta densidad de almacenamiento y el espacio reducido que ocupa el ASRS, lo que permite a Asahi consolidar todas sus operaciones en un único emplazamiento. Esto supone un ahorro de costes gracias a la reducción de alquileres, una menor complejidad en el servicio a sus clientes, menos palés revueltos que pueden provocar daños y errores, menores costes de transporte y tiempos de entrega más rápidos.
"Un sistema automatizado como éste elimina gran parte de la manipulación manual de los palés", afirma Dominic. "Esto no sólo crea eficiencias y un gran aumento de la productividad del 250% para el cliente, sino que también aumenta la seguridad de los trabajadores al no tener tantas carretillas elevadoras".
En un centro de distribución como el de Asahi en Heathwood, cada manipulación manual de un palé representa un coste para la empresa y conlleva el riesgo de un error humano.
Desde que automatizó sus procesos de almacén y sólo utiliza procesos manuales cuando tiene sentido, la mayoría de los palés de Asahi no son tocados por una persona hasta que llegan al centro de distribución del cliente.
"Cuando pensamos en la cantidad de toques que se producen en un proceso de almacén, cada uno de ellos supone un coste para su negocio", afirma David Rubie, Industry Manager F & B Manufacturing, Dematic. "Así que tener ese proceso automatizado y utilizar el trabajo manual sólo cuando tiene más sentido es una forma realmente fantástica de dirigir una empresa de logística".
"Cuando estábamos diseñando las instalaciones para Asahi y considerando la ocupación prevista, Dematic calculó que deberíamos optar por una ocupación global de las operaciones de alrededor del 89%", añadió David. "Nos complace ver que Asahi está superando eso ahora con una ocupación del 90 al 92% en toda la instalación".
Preparados para el futuro
Dematic ha proporcionado a Asahi apoyo continuo con técnicos de servicio in situ para garantizar el éxito del sistema ASRS en el centro de Heathwood.
"Los técnicos residentes de Dematic han sido fundamentales para el éxito y el buen funcionamiento de nuestro centro", dijo Nathan. "La relación que mantienen con nuestros equipos de turno de Asahi es fantástica. Su comunicación y su trabajo para comprender nuestras limitaciones operativas han sido de primer nivel."
Contar con el apoyo de Dematic durante todo el proyecto ha ayudado a Asahi a ampliar sus propios conocimientos sobre el funcionamiento de la automatización, especialmente ASRS. Esto les ha permitido sacar el máximo partido de su nueva solución y garantizar que el centro de distribución de Heathwood siga funcionando con la mayor eficiencia posible.
"Una de las cosas que me entusiasma de sistemas como el ASRS es que va a ser seguro para nuestros trabajadores del centro de distribución", añade Nathan. "Con el sistema automatizado, las operaciones de nuestro almacén funcionan como un reloj, ya no es necesario que tantos trabajadores realicen tareas manuales".
"La implantación del ASRS nos ha preparado para el futuro. Y ciertamente estoy orgulloso de lo que hemos conseguido aquí junto con Dematic."