Polaris cambia marcia grazie al nuovo centro di distribuzione
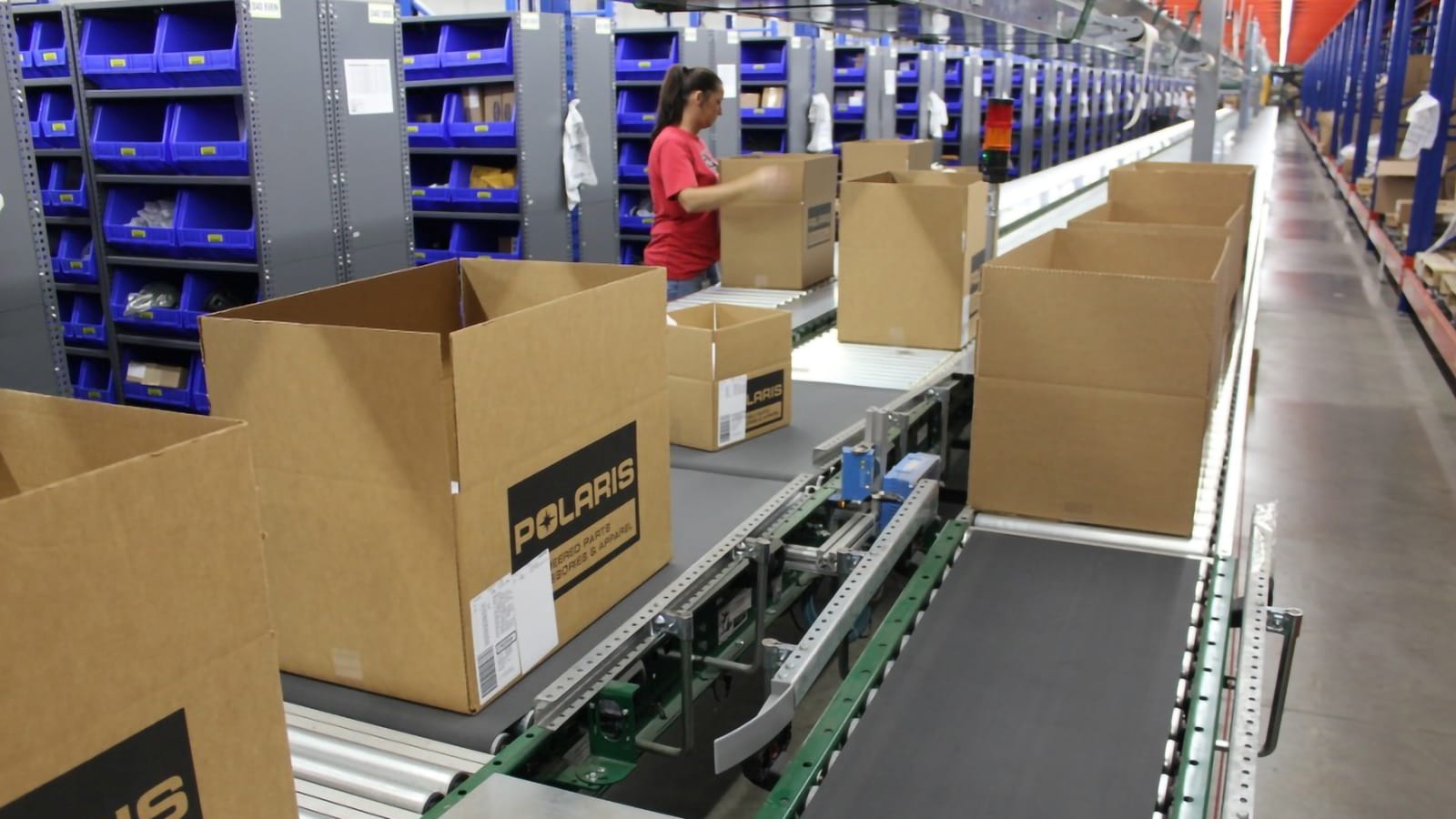
6 agosto 2022
Polaris Industries, azienda produttrice di veicoli da strada e off-road, motoslitte e motociclette, supporta gli appassionati di motori e gli addetti ai lavori offrendo veicoli e servizi innovativi e di alta qualità. Per rifornire i rivenditori di pezzi e accessori, Polaris ha progettato, costruito e implementato un nuovo centro di distribuzione dedicato ai rivenditori dell'America Nord-orientale.
Panoramica
Per venire incontro alle alte aspettative dei propri rivenditori e assicurare che gli ordini siano elaborati con velocità, precisione ed efficienza, Polaris aveva bisogno di una soluzione che ottimizzasse i processi di raccolta, imballaggio e spedizione. Secondo Paul Eickhoff, Direttore delle Operazioni di Polaris, "il nostro vantaggio principale è la nostra cultura innovativa, la velocità operativa e la flessibilità, oltre alla passione per continuare a migliorare la catena di fornitura e distribuzione dei pezzi".
Le sfide
In precedenza, Polaris riforniva pezzi e accessori ai suoi rivenditori della parte orientale degli Stati Uniti dal suo centro di Vermillion, nel South Dakota. Per ottimizzare i servizi e i tempi di risposta per questi rivenditori e supportare la futura crescita aziendale, era necessaria una nuova struttura di distribuzione. Da un punto di vista dell'efficienza della rete, è stato individuato l'Ohio come posizione geografica ideale. È stato acquistato un edificio esistente ed è così che è nato un nuovo centro di distribuzione di Polaris.
La soluzione
Il centro di distribuzione si affida a un piano di localizzazione strategico dell'inventario per ottimizzare le prestazioni operative. I pezzi di Polaris da raccogliere nei contenitori vengono centralizzati nel modulo di raccolta dei contenitori pieni. I pezzi da raccogliere come "pezzi" vengono centralizzati nel modulo di raccolta dei contenitori frazionati. Gli articoli grandi, a bassa velocità e non trasportabili sono posizionati insieme in dei pallet sulle scaffalature. Inoltre, gli SKU vengono distribuiti in queste aree in base alla velocità.
Il modulo di raccolta a contenitori frazionati si basa su una metodologia che porta il contenitore dell'ordine all'operaio. Questo metodo è definito Sistema di instradamento a zone. I lavoratori restano in una zona assegnata. Si ottiene maggiore efficienza in quanto i lavoratori non girano per il magazzino per cercare i pezzi, ma devono concentrarsi a raccogliere un segmento dell'inventario localizzato in un luogo ben definito e compatto.
Il modulo di raccolta a contenitori frazionati è formato da 4 zone. In ogni zona, gli SKU vengono sistemati su degli scaffali o strutture di flusso. Le zone sono suddivise in base agli attributi come la natura del pezzo, la velocità o l'utilizzo delle cubature. Il metodo operativo consiste nel far girare il contenitore dell'ordine solo nelle zone in cui è prevista la raccolta.
Per supportare il metodo di raccolta con Sistema di instradamento a zone, viene garantita una rete di trasportatori per controllare il flusso dei cartoni degli ordini in ingresso e in uscita dalle zone. In ogni zona si trova un lavoratore, tuttavia è possibile aggiungere ulteriori lavoratori durante i periodi di picco lavorativo. Oppure, durante i periodi con volumi di ordini ridotti, un solo lavoratore può gestire più zone.
La struttura del trasportatore prevede un trasportatore di accumulo che gira attraverso l'intero modulo di raccolta dei contenitori frazionati con un'uscita e un raccordo per ogni zona. In ogni punto di uscita è presente un lettore di codice a barre e un trasferimento ad angolo retto per indirizzare il contenitore dell'ordine verso la zona di raccolta. Quando la raccolta è completata, l'operatore spinge il cartone dell'ordine di nuovo verso la struttura centrale del trasportatore. In caso di ulteriori raccolte, si sposta verso un'altra zona; altrimenti, si dirige direttamente all'imballaggio sul trasportatore centrale.
La stazione di lavoro di avvio dell'ordine si trova a monte del trasportatore centrale nel modulo di raccolta dei contenitori frazionati. Il lavoratore applica un'etichetta con codice a barre unico per ogni cartone, forma il cartone e lo inserisce nella macchina di applicazione del nastro in linea. Il cartone procede verso il trasportatore centrale verso la zona in cui si trova l'inventario dell'ordine.
I lavoratori che stazionano nelle zone utilizzano dei dispositivi RF mobili per ottenere le istruzioni di raccolta. Quando un contenitore dell'ordine arriva nella zona di raccolta, il lavoratore scansiona il codice a barre sul contenitore dell'ordine utilizzando il dispositivo RF. Dopodiché, compaiono le istruzioni di raccolta sullo schermo. Nella posizione di raccolta, il lavoratore scansiona il codice a barre dello SKU sul prodotto per confermare l'esattezza dello SKU. Gli articoli vengono prelevati e posti nel cartone dell'ordine. Il cartone dell'ordine viene spinto manualmente di nuovo verso la struttura centrale del trasportatore.
Ogni contenitore dell'ordine a raccolta separata viene convogliato verso il sotto-sistema di imballaggio e spedizione. Nella stazione di imballaggio, viene verificata la precisione dell'ordine, si esegue il peso per il calcolo dei costi di spedizione, si applica un'etichetta di spedizione e il cartone viene sigillato. Questi cartoni di ordini con contenitori frazionati vengono convogliati verso l'area di spedizione in cui un sistema suddivide automaticamente in cartoni verso la piattaforma di spedizione adeguata per un caricamento fluido dei camion. I cartoni per le spedizioni LTL vengono indirizzati automaticamente verso una stazione di pallettizzazione manuale.
Il modulo di raccolta dei contenitori pieni è formato da pallet con contenitori posizionati su una struttura a scaffale. In base alle istruzioni del dispositivo RF portatile, il lavoratore si dirige verso la posizione del pallet e raccoglie i contenitori inserendoli sul trasportatore che opera al centro del modulo di raccolta dei contenitori pieni. Ad ogni contenitore viene affrancata un'etichetta prestampata. I contenitori dei moduli di raccolta dei contenitori pieni vengono indirizzati verso la spedizione e quindi instradate automaticamente verso l'autotrasportatore adeguato per un carico fluido o verso la zona di pallettizzazione e spedizione LTL.
Il software del Sistema di controllo del magazzino gestisce le operazioni automatizzate dell'intera rete di trasporto e distribuzione. Questo software modulare indirizza il flusso degli ordini con contenitori frazionati nelle zone di raccolta adeguate. Utilizzando i dati dei lettori dei codici a barre, il software attiva i dispositivi di trasferimento ad angolo retto adeguati per permettere ai cartoni di passare automaticamente alle zone di raccolta.
Inoltre, il software WCS dirige le operazioni e il controllo del sotto-sistema di trasporto del modulo di raccolta dei contenitori pieni, delle stazioni di imballaggio e del sotto-sistema di distribuzione delle spedizioni. Sono disponibili informazioni in tempo reale riguardo la posizione dei cartoni nel sistema, statistiche di ordinamento/distribuzione, tassi di lettura dei codici a barre e ricircolo dei cartoni. Una rappresentazione grafica del sistema mostra informazioni in tempo reale riguardo lo stato e gli attributi di prestazione di ogni sotto-sistema: raccolta, imballaggio, unione degli imballaggi, linea dei rifiuti e spedizione.
I risultati
Il sistema a struttura modulare favorisce l'efficienza operativa, la velocità di elaborazione degli ordini e la precisione degli stessi, garantendo al contempo la flessibilità di venire incontro alle modifiche dei requisiti quotidiani. La capacità di elaborazione degli ordini può essere scalata aumentando il numero di lavoratori nei moduli per contenitori frazionati e pieni durante i periodi di picco lavorativo. Durante i periodi di minore attività, è possibile assegnare meno lavoratori per gestire il volume degli ordini. Inoltre, le stazioni di lavoro e i convogliatori degli sportelli di spedizione possono essere attivati o disattivati in base alle attività quotidiane. L'attività attuale si attesta su circa 500-700 ordini al giorno (6.000 linee) con circa 150 ordini di rifornimento di inventario. La capacità del sistema è di 25.000 linee.
Lo staff di raccolta non è obbligato a circolare lungo l'intero magazzino per localizzare l'inventario per la raccolta. Al contrario, il sistema designa delle posizioni per i lavoratori nelle zone di raccolta in cui l'inventario viene organizzato in una configurazione compatta e ad alta densità. Ciò permette ai lavoratori di camminare meno e portare a termine un maggior numero di raccolte ogni ora. Inoltre, il Sistema di instradamento a zone dirige i contenitori degli ordini solo verso zone con raccolte, riducendo pertanto i tempi di elaborazione degli ordini. L'approccio sistemico, combinato con l'automazione di trasporto e distribuzione, garantisce disciplina, miglioramento dei processi e produttività sul lavoro nei processi di raccolta, imballaggio e spedizione. Inoltre, il sistema è pensato per favorire la crescita. Ad esempio, i distributori sono pre-installati nella struttura di spedizione. In futuro, quando sarà richiesta una maggiore capacità, sarà possibile collegare una linea di trasporto modulare e attivare il software pre-configurato.