Nieuw Asahi-magazijn bereikt 250% productiviteitsstijging met geautomatiseerd systeem
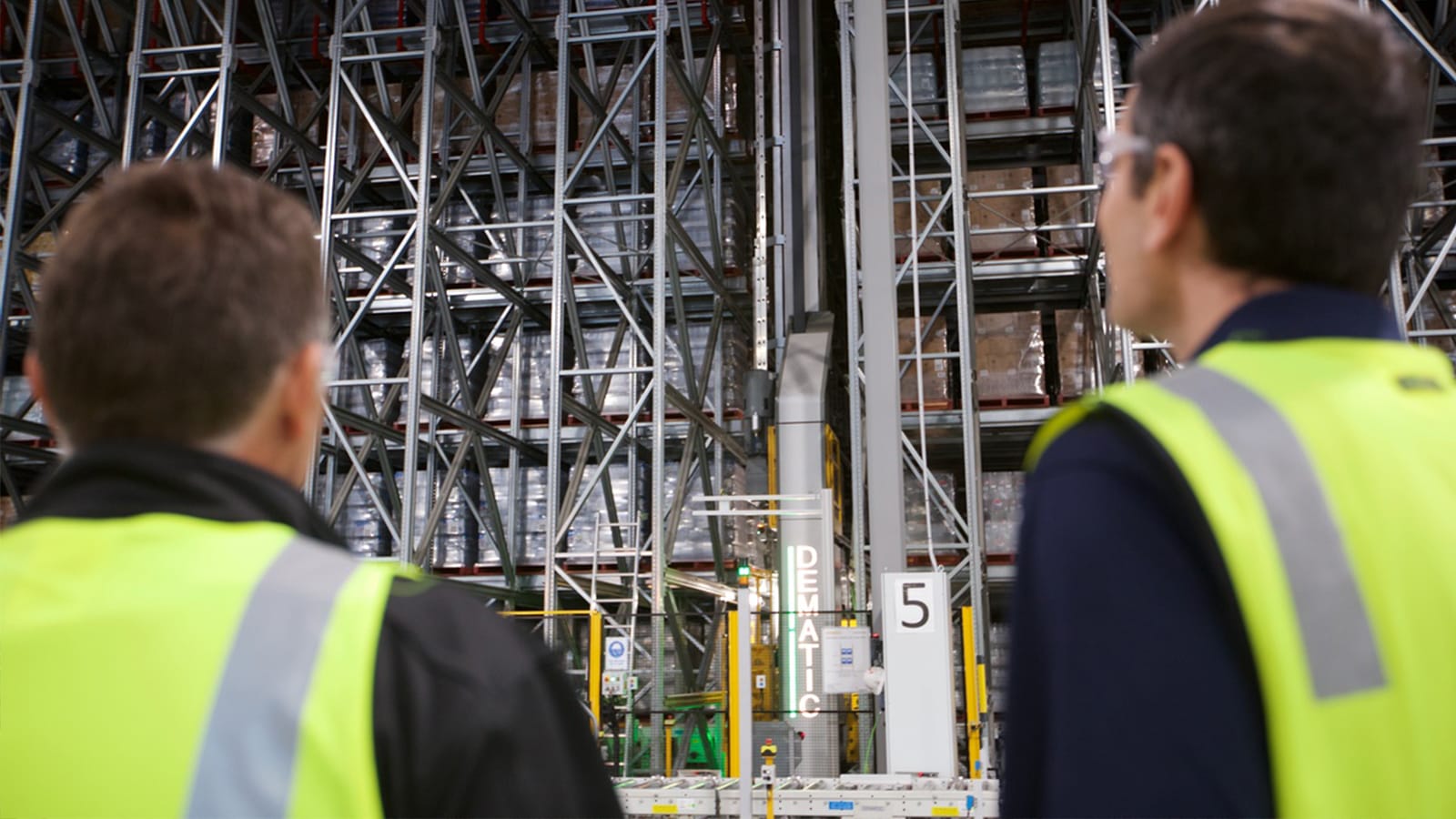
Asahi Beverages is een toonaangevend drankenbedrijf dat alcoholische en niet-alcoholische producten produceert en distribueert in Australië en Nieuw-Zeeland. Asahi heeft een rijke en gevarieerde geschiedenis, brengt kwaliteitsdranken op de markt en heeft een sterke portfolio van gevestigde merken en innovatieve, nieuw gelanceerde producten.
Asahi Beverages maakt deel uit van Asahi Group Holdings, een van de grootste drankenproducenten van Japan, en omvat enkele van de meest succesvolle drankenproducenten van Australië en Nieuw-Zeeland, zoals Asahi Lifestyle Beverages (voorheen bekend als Schweppes Australia), Asahi Premium Beverages, Independent Liquor en The Better Drinks Co.
Vandaag de dag heeft Asahi Beverages meer dan 2100 mensen in dienst in Australië en Nieuw-Zeeland.
Overschakelen van een handmatig systeem
Asahi heeft een aantal distributiecentra in Australië. Voorheen werkte Asahi vanuit meerdere locaties in Brisbane en maakte het gebruik van handmatige vorkheftrucks voor blokstapeling, wat veel nadelen en uitdagingen met zich meebracht.
Asahi heeft onlangs zijn locaties in Brisbane samengevoegd tot één centraal magazijn. Met de ontwikkeling van het centrale magazijn in Heathwood besloot Asahi over te stappen op een geautomatiseerde opslagoplossing, omdat het bedrijf voorheen een zeer arbeidsintensief systeem gebruikte.
“Elke vrachtwagen die aankwam, moest worden uitgeladen met een vorkheftruck, vervolgens moesten we handmatig het papierwerk ontvangen, handmatig de pallets controleren, de pallets naar de opslaglocatie verplaatsen en dat alles vervolgens in omgekeerde volgorde doen om ze te verzamelen”, zegt Nathan Lucinsky, DC Manager Heathwood, Asahi.
Met de beslissing om de locaties te consolideren in één distributiecentrum en over te stappen op een geautomatiseerde oplossing, wilde Asahi een aantal voordelen behalen, waaronder kostenbesparingen, efficiëntie- en productiviteitsstijgingen en de mogelijkheid om beter aan de behoeften van de klanten te voldoen.
Automatisch opslagsysteem
Een belangrijke factor in het besluitvormingsproces van Asahi bij het zoeken naar een geautomatiseerde opslagoplossing om aan de vereisten van Heathwood DC te voldoen, was het werken met een bedrijf dat de lokale markt kende. Asahi koos voor Dematic vanwege het bewezen vermogen van het bedrijf om soortgelijke projecten in Australië te realiseren.
“Aangezien de nieuwe automatiseringsoplossing een eerste implementatie was, was het voor Asahi van cruciaal belang om het goed te doen,” aldus Dominic Figliano, Project Manager bij Dematic. “Tijdens de eerste ontwerp- en conceptontwikkelingsfase heeft Dematic een aantal alternatieven voor lage en hoge schappen overwogen, maar na het beoordelen van de opslagvereisten van Asahi wisten we dat de beste oplossing voor hen het geautomatiseerde opslagsysteem (ASRS) met zesdelige satellietopslag was.
Het hoogbouwmagazijn van Asahi Heathwood DC is 13 verdiepingen hoog en 34 opslaglocaties diep. Het ASRS strekt zich uit tot zes palletlocaties diep aan elke kant van de zes kranen, die toegankelijk zijn via satellietwagens. In totaal zijn er ongeveer 31.500 palletplaatsen.
“Het geautomatiseerde magazijn dat we voor Asahi hebben gebouwd, maakt gebruik van de nieuwste en snelste kraan van Dematic, de 1200-1, die ook het hoogste satellietsysteem is dat we in Australië hebben gebouwd,” aldus Dominic.
De reis van een pallet begint op een van Asahi's twee productielocaties in Queensland. Vervolgens wordt het product per vrachtwagen vervoerd naar Heathwood DC. Wanneer de vrachtwagen op de locatie aankomt, rijdt de chauffeur achteruit de schaatshelling op en activeert dan het automatische apparaat om de trailer uit te lijnen en het losproces te starten. De skates rijden de achterkant van de trailer in, de luchtkussens worden losgelaten en de pallets worden van de vloer van de trailer getild.
Op dit punt keren de skates terug naar de helling, laten de luchtkussens leeglopen en transporteren kettingtransporteurs de pallets naar onze hoofdtransportband in het magazijn.
De pallets doorlopen dan een geautomatiseerde profielcontrole waar ze worden gevalideerd aan de hand van de specificatievereisten van het opslagsysteem. De conveyor loop levert de pallet naar het afleverstation waar het ASRS systeem het overneemt.
De stapelkraan tilt de pallet op en verplaatst hem naar de toegewezen opslaglocatie, waarna een supercap trolley de pallet oppakt en naar de satelliet brengt om hem daar op te slaan.
Het geautomatiseerde magazijn wordt bestuurd door de Dematic WCS-software. Operators werken met het WCS GUI-systeem in de automatische controlekamer en ook op de werkstations in de faciliteit, en ze hebben ook het voordeel van een SCADA-systeem waarmee ze de status van het systeem in realtime kunnen volgen.
Naast het hoogbouwmagazijn integreerde Dematic ook apparatuur van derden, waaronder de skate docks, een rekwikkelaar, automatische etiketteerders en een palletomvormer.
Die Einführung des Systems
Vor dem Bau des Zentrallagers in Heathwood war Dematic an der Auswahl eines neuen Standorts für das neue Zentrallager beteiligt, um sicherzustellen, dass der Standort den Lageranforderungen von Asahi sowie den Anforderungen des von Dematic entwickelten neuen Systems entspricht.
"Als wir mit der Installation des Lagers begannen, befand sich das Rechenzentrum von Asahi noch auf der grünen Wiese, was eine Reihe von Herausforderungen mit sich brachte", so Dominic. "Da das DC noch eine Baustelle war, gab es Bauarbeiter, Elektriker, Betonierer und andere Auftragnehmer und Arbeiter vor Ort, mit denen wir uns abstimmen und zusammenarbeiten mussten. So mussten wir uns beispielsweise eng mit der Installation der Sprinkleranlage abstimmen, um sicherzustellen, dass die Sprinkler in die Regale passen und den Anforderungen entsprechen."
Eine enge Koordinierung und Zeitplanung war ebenfalls von entscheidender Bedeutung, um die verschiedenen Geräte, die von den verschiedenen Arbeitern eingesetzt wurden, so zu koordinieren, dass die Projektfristen eingehalten werden konnten. Dematic hatte zwei Teams vor Ort, die bis zu zwei 80-Tonnen-Kräne, vier Ausleger- und zwei Scherenhebebühnen einsetzten.
"Wir hatten bis zu 50 Leute vor Ort und haben einen Teil der Installation in der Nacht durchgeführt, um den Zeitplan einzuhalten und das Projekt pünktlich abzuschließen.
Ein weiterer wichtiger Aspekt der Systemeinführung war die Schulung, die Dematic für das Asahi-Team nach Abschluss der Installation durchführte.
"Wir boten Asahi eine Superuser-Schulung an, bei der wir in kleinen Gruppen sowohl theoretische als auch praktische Schulungen zur Nutzung des neuen Systems durchführten. Diese Superuser konnten dann in Zukunft andere Mitarbeiter von Asahi schulen", so Dominic.
Da das Heathwood DC über Hochregallager verfügt, wurde ein zusätzlicher Schwerpunkt auf die Sicherheit bei Arbeiten in der Höhe gelegt.
Der Rollout des neuen Systems wurde im Mai 2019 erfolgreich abgeschlossen.
Voordelen van het nieuwe systeem
De grote voordelen van het Dematic-systeem zijn de hoge opslagdichtheid en het kleinere vloeroppervlak van de stapelkraan, waardoor Asahi zijn hele operatie op één locatie kan consolideren. Dit resulteert in kostenbesparingen door lagere huurkosten, minder complexiteit bij de klantenservice, minder pallettransfers die kunnen leiden tot schade en fouten, lagere transportkosten en snellere doorlooptijden van vrachtwagens.
“Een geautomatiseerd systeem als dit elimineert een groot deel van de handmatige verwerking van pallets,” zegt Dominic. “Dit zorgt niet alleen voor efficiëntie en een hoge productiviteitsstijging van 250% voor de klant, maar verhoogt ook de veiligheid voor de werknemers omdat er minder vorkheftrucks nodig zijn.”
In een distributiecentrum zoals dat van Asahi in Heathwood is elke handmatige aanraking van een pallet een kostenpost voor het bedrijf en brengt het risico van een menselijke fout met zich mee.
Sinds Asahi zijn magazijnprocessen heeft geautomatiseerd en alleen nog handmatige processen gebruikt waar dat zinvol is, worden de meeste pallets niet meer aangeraakt door een mens totdat ze het DC van de klant bereiken.
“Als je bedenkt hoeveel aanrakingen er zijn in een magazijnproces, is elke aanraking een kostenpost voor het bedrijf,” zegt David Rubie, Industry Manager F&B Manufacturing, Dematic. “Dat proces automatiseren en alleen handmatige arbeid gebruiken wanneer dat zinvol is, is echt een goede manier om een logistiek bedrijf te runnen.”
“Toen we de faciliteit voor Asahi ontwierpen en keken naar het verwachte gebruik, berekende Dematic dat we moesten streven naar een algehele bezettingsgraad van ongeveer 89%,” voegt David toe. “We zijn verheugd dat Asahi dit nu overtreft met een bezettingsgraad van 90 tot 92% in de hele fabriek.”
Uitgerust voor de toekomst
Dematic heeft Asahi voortdurend ondersteund met on-site servicetechnici om het succes van het geautomatiseerde magazijn in het distributiecentrum in Heathwood te garanderen.
“De plaatselijke Dematic-technici zijn van cruciaal belang geweest voor het succes en de soepele werking van onze locatie,” zegt Nathan. “De relatie die zij hebben met onze Asahi-ploegteams is fantastisch. Hun communicatie en hun inspanningen om onze operationele beperkingen te begrijpen waren eersteklas.”
De ondersteuning van Dematic gedurende het project heeft Asahi geholpen om hun eigen kennis van de werking van automatisering te vergroten, met name van magazijnen. Dit heeft hen in staat gesteld om het meeste uit hun nieuwe oplossing te halen en ervoor te zorgen dat het Heathwood DC zo efficiënt mogelijk blijft werken.
“Een van de dingen waar ik enthousiast over ben, is dat systemen zoals magazijnkranen veilig zijn voor ons magazijnpersoneel,” voegt Nathan toe. “Met het geautomatiseerde systeem lopen onze magazijnprocessen op rolletjes en is er niet langer behoefte aan zoveel arbeiders die handmatige taken uitvoeren.”
“De introductie van het geautomatiseerde magazijn heeft ons klaargestoomd voor de toekomst. En ik ben echt trots op wat we hier samen met Dematic hebben bereikt.”